Cadel – La nuova Fabbrica integrata in ottica 4.0
- Home
- Case Studies
- CADEL – La nuova Fabbrica integrata in ottica 4.0
L'azienda e le necessità
Fondata nel 1949, Cadel è un’azienda italiana che progetta e costruisce stufe di qualità. Entrata a far parte del Gruppo MCZ nel 2013, offre una gamma completa di stufe a pellet ventilate, canalizzate e idro. Da oltre sessant’anni interpreta le esigenze e i bisogni delle famiglie, realizzando una varietà di prodotti dal design distintivo ma economicamente accessibili e di semplice utilizzo. Un’azienda Made in Italy che mantiene i valori della tradizione guardando al futuro.
Questo costante sguardo verso il progresso ha richiesto la progettazione di un nuovo sito produttivo. Infatti, la nuova Fabbrica Integrata che sorge a Santa Lucia di Piave (TV), è stata realizzata per poter sostenere la costante crescita dell’azienda. La soluzione 4.0 non risulta essere solo altamente tecnologica, affidabile e all’avanguardia ma anche modulabile nel tempo. È stato infatti studiato ed implementato un impianto flessibile ed in grado di soddisfare le necessità in continuo divenire ed eventuali future espansioni.
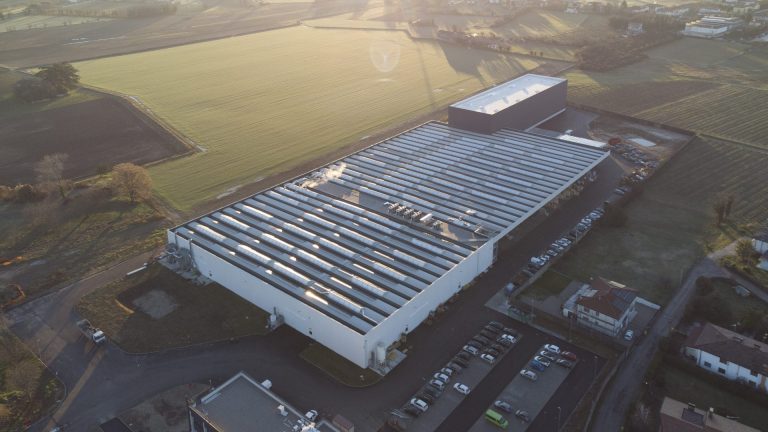
Il progetto realizzato
A seguito delle analisi effettuate, LCS ha ingegnerizzato una soluzione 4.0 che comprende un magazzino automatico autoportante, 10 linee di produzione, 8 linee di finitura ed un impianto composto da 9 AGV.
Il nuovo polo, che vanta circa 18.000 mq di area, è al servizio dell’intero processo produttivo per la costruzione del prodotto finale. Dalla materia prima si arriva alla costruzione e alla personalizzazione della stufa sulle linee di produzione e finitura, si passa allo stoccaggio nel magazzino automatico fino ad arrivare alla spedizione verso rivenditori al dettaglio e/o GDO.
All’interno della nuova fabbrica si sviluppano diversi flussi operativi identificati che possono essere così suddivisi:
- I semilavorati, provenienti dalle linee di produzione, vengono stoccati in magazzino oppure dal magazzino convergono verso le linee di finitura
- Il prodotto finito, proveniente dalle linee di finitura, viene destinato allo stoccaggio in magazzino
- Il prodotto finito viene destinato alla personalizzazione e poi stoccato in magazzino pronto per la spedizione
- I Kit di montaggio, provenienti da fornitori esterni, sono destinati alla personalizzazione oppure allo stoccaggio in magazzino
- Il prodotto finito viene destinato alla spedizione
Magazzino automatico e impianto AGV
Il magazzino automatico presenta una struttura autoportante alta 21 metri con 10 livelli di stoccaggio, 3 corridoi serviti da altrettanti traslo-elevatori per una giacenza totale di quasi 17.300 ubicazioni riservate alle sette tipologie di UdC presenti.
Lo stoccaggio avviene in doppia profondità per i pallet e in quadrupla profondità per i mezzi pallet.
Il progetto è stato pensato in modo da poter espandere in futuro il magazzino ed aumentare la capacità di stoccaggio fino a oltre 23.000 ubicazioni.
Su ciascun ingresso a magazzino è presente un controllo sagoma; mentre su ciascuna uscita sono presenti due etichettatrici per l’etichettatura dei pallet destinati alla spedizione.
Il magazzino automatico è collegato alle diverse aree della fabbrica tramite una flotta di 9 AGV che si muovono grazie ad un sistema a induzione annegato nel pavimento. Questo trasferimento di energia elettrica senza contatto permette non solo la guida e l’alimentazione dei veicoli durante la marcia ma garantisce benefici anche in termini di sostenibilità ambientale grazie all’eliminazione delle batterie al litio (gestione e smaltimento).
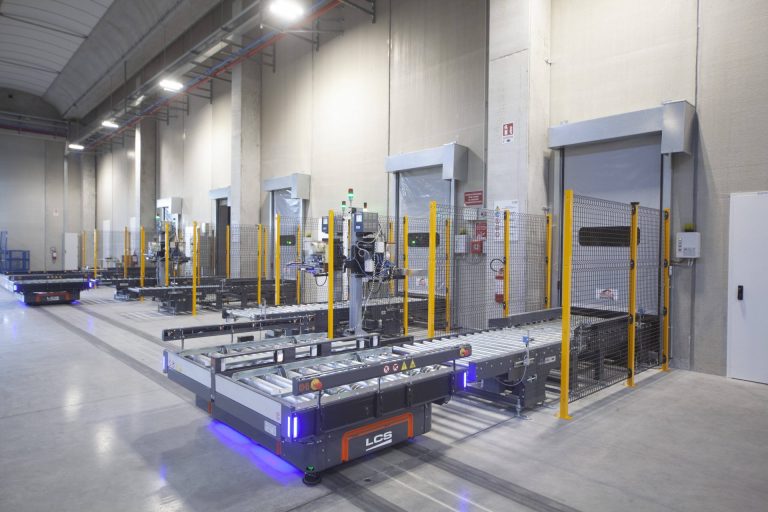
Linee di produzione
La produzione delle stufe avviene su 10 linee di montaggio dei semilavorati, 7 linee per la finitura del prodotto e 1 linea per il kittaggio (personalizzazione).
Le linee di montaggio sono configurate in modo da poter suddividere le varie fasi di assemblaggio fino ad un massimo di 6 operatori mentre le linee di finitura e kittaggio sono configurate in modo da avere una linea corta, con 1 operatore, e una linea lunga, con 2 operatori ciascuna.
Tutte le linee sono configurabili e gestite dal software di LCS in base alla tipologia di stufa da produrre.
Il software
Per consentire al cliente di tracciare i pallet movimentati e ridurre al minimo gli errori umani derivanti dalle operazioni di identificazione e movimentazione a terra dei pallet, è stato implementato un sistema articolato di lettori RFID installati su tutti i punti di ingresso e uscita al sistema e gestiti dal Software LCS.
I pallet sono dotati di etichetta con barcode e tag RFID, applicati dal primo operatore di ciascuna linea di montaggio in base all’ordine di produzione, e controllati in ogni passaggio produttivo, dal montaggio alla finitura, dallo stoccaggio alla spedizione.
Viene quindi garantita la tracciabilità in tempo reale dei materiali movimentati all’interno dello stabilimento.
La matricola della stufa, e con essa i componenti che la compongono vengono associati al tag RFID dal sistema informativo aziendale garantendo la rintracciabilità dei materiali anche dopo la consegna al cliente.
Sono inoltre stati previsti dei gate RFID sulle ribalte di attracco dei mezzi di trasporto, mediante i quali viene certificato il corretto carico dei bilici.
In questo modo anche la logistica ha modo di controllare in modo rapido ed efficace l’avvenuto carico e la chiusura dei documenti di viaggio, prima che i camion partano dallo stabilimento.
Il software WMS LogiWare gestisce, in collegamento diretto con l’ERP del cliente, tutto il magazzino automatico mentre il sistema LogiCon/LogiDrive, connesso al sistema LogiWare, permette la supervisione ed il controllo dell’intero impianto.
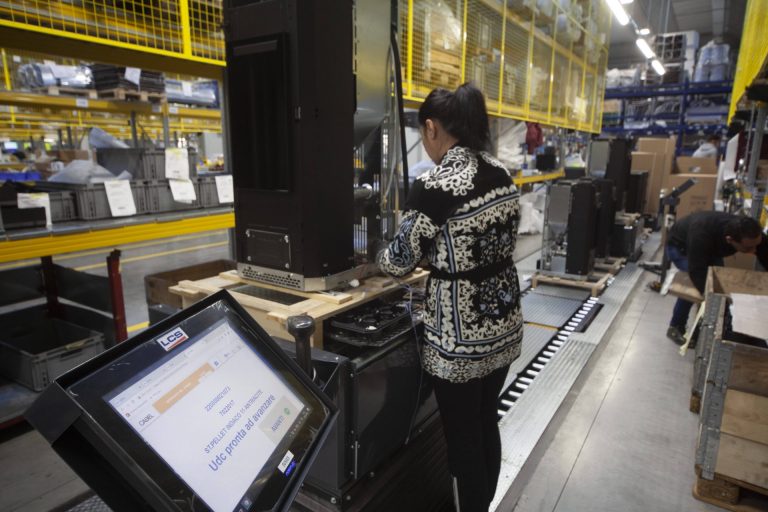
Benefici ottenuti
Con il Cliente è stata studiata e realizzata una vera e propria Fabbrica Intelligente in ottica 4.0, che ha consentito di ottenere benefici e miglioramenti fin da subito tangibili:
- Integrazione in un unico sito dell’intero processo produttivo delle stufe;
- Maggiore efficienza produttiva e gestione dei flussi operativi;
- Tracciabilità costante e controllo delle UdC tramite il sistema RFID;
- Ottimizzazione degli spazi e maggiori capacità di stoccaggio;
- Automazione nella movimentazione delle merci;
- Riduzione importante dei costi.