La logistica prende a prestito la filosofia dei pit-stop di Formula Uno per organizzare la ristrutturazione di un magazzino automatico in pochi giorni e senza impattare sull’operatività quotidiana.
La logistica, come si sa, è un’attività trasversale che interessa la maggior parte dei processi industriali.
Negli anni su questo aspetto abbiamo avuto modo di scrivere più e più volte. In diverse occasioni abbiamo sottolineato come le attività di gestione di una supply chain siano ormai diventate parte integrante di innumerevoli settori e, in altrettante, abbiamo avuto modo di analizzare, speriamo con il dovuto dettaglio, contesti operativi di ogni genere e forma.
Abbiamo raccontato le più diverse catene di fornitura, da quella dell’elettronica a quella dei ricambi per betoniere, da quella dell’abbigliamento a quella degli articoli sportivi. Ci siamo confrontati con gli schemi, le procedure e le tecnologie più disparate.
Siamo entrati nei magazzini dove venivano movimentati prodotti piccoli e leggeri, grandi e pesanti, solidi e liquidi, e abbiamo visto come si svolgono le attività di picking a 40 gradi sotto zero. Mai però ci eravamo imbattuti in un magazzino automatico con misure da gigante, dove l’unità di carico è un gingillo alto più di 2 metri dal peso di circa 5 tonnellate.
Ma il bello della logistica è proprio questo: la trovi ovunque, anche laddove, pur cosciente della sua trasversalità, non avevi ancora pensato.
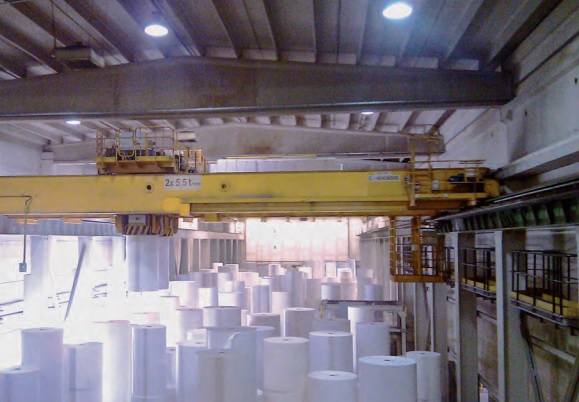
PESANTI COME DOLMEN
È il caso, ad esempio, della catena di fornitura di carta patinata. L’uso classico di questo tipo di carta è per le riviste, calendari, depliants e tutto ciò che richiede un tipo di carta di qualità superiore rispetto alla media. Com’è logico aspettarsi, non nascono già tagliate e confezionate.
Alle spalle di quel supporto sul quale troviamo foto, prodotti, notizie, c’è una filiera articolata che, partendo dall’unione di carbonato (polvere di marmo) e cellulosa, attraverso un processo a ciclo continuo, sforna come semilavorati lunghissimi rotoli di varie dimensioni che poi, avvolti su bobine, servono ad alimentare le macchine per il taglio dei vari formati, standard e non.
Ora, provate ad immaginare di porvi nel punto esatto in cui la linea di produzione incontra quella dedicata al taglio, cioè dove i tempi e le logiche push che dominano a monte incrociano i tempi e le logiche pull che governano invece i processi a valle, inevitabilmente più a contatto con il mercato e le sue necessità.
Ecco, in quel posto, è evidente, occorre uno spazio, una sorta di camera di compensazione che consenta di accoppiare e sincronizzare flussi altrimenti inconciliabili. Serve, in pratica, un magazzino.
Però, badate, non un magazzino qualsiasi. Per muovere blocchi di carta pesanti come dolmen e candidi come la neve, il classico duetto scaffalatura-carrello elevatore non è proprio l’ideale. E men che meno lo è dal momento in cui, oltre a dover tener conto del fattore spazio e della necessità di non danneggiare il prodotto, è soprattutto indispensabile tener conto del fattore tempo.
Quello di cui stiamo parlando, infatti, non è un deposito di fine linea dove la merce staziona prima della fase distributiva. Qui siamo nel bel mezzo di un processo produttivo che gira 24 ore su 24, 7 giorni su 7, senza soluzione di continuità. Questo significa che un ritardo, un rallentamento o anche un piccolo intoppo a metà del guado si ripercuote come un’onda d’urto in tutta la filiera, in un senso e nell’altro, provocando un effetto domino dagli esiti difficilmente prevedibili.
IL MAGAZZINO ENTRA AI BOX
Descritto il contesto, provate ora a pensare di essere chiamati ad intervenire su un simile colosso con più di trent’anni di duro lavoro sulle spalle e di dover fare tutto quanto è necessario per aggiornarne le strutture e le performance senza bloccare il ciclo produttivo, come in un pit stop di Formula Uno.
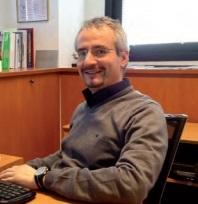
Ecco, questa è la sfida che si è trovata di fronte la LCS di Usmate (MB), il system integrator che, nell’ambito di un progetto con Demag come main contractor, si è occupato della ristrutturazione e del rinnovo del magazzino automatico bobine di Cartiere del Garda (Riva del Garda – TN).
Una sfida, ci spiega Fabio Zucchini, Chief Technical Officer di LCS, giocata sul filo dei secondi, in cui ogni singola operazione, come avviene nei box di un Gran Premio, era stata precisamente temporizzata e collocata su un calendario lavori che non dava spazio ad alcun margine di errore.
“Dieci giorni – sottolinea Zucchini -, questo era il tempo che avevamo a disposizione per sostituire le parti usurate, riammodernare l’impiantistica e la climatizzazione, cambiare tutti i motori e conseguentemente gli azionamenti, portare l’alimentazione da 500 a 400 volt, montare una serie di telecamere, installare i software di gestione e controllo (WMS e WCS), rimpiazzare i vecchi sistemi di comunicazione via cavo con dispositivi wireless e, soprattutto, ripensare il sistema di rilevatori laser che consente all’impianto di lavorare anche con pochi centimetri di scarto”.
E, come se tutto questo non bastasse a rendere il progetto sufficientemente “stimolante”, ogni cosa si sarebbe dovuta svolgere a magazzino pieno, senza cioè spostare nulla di quanto al suo interno stoccato.
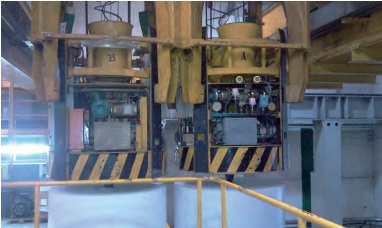
INTERVENTO A CUORE APERTO
Lavorando senza sosta, 365 giorni l’anno, con un prodotto delicato come la carta, infatti, Cartiere del Garda non poteva permettersi né di bloccare il ciclo produttivo per troppo tempo né, tantomeno, di svuotare il magazzino automatico, non fosse altro perché un simile approccio avrebbe comportato la necessità di trovare un altro magazzino in cui collocare per tutto il tempo necessario uno stock piuttosto ingombrante come il suo.
Quindi, in sostanza, ogni cosa andava fatta “in corsa”.
Da qui la scelta di fare una sorta di operazione a cuore aperto durante una specie di sosta tecnica da collocare in un periodo dell’anno, agosto, in cui un’eventuale interruzione del ciclo produttivo, se prevista e rispettata con precisione svizzera, non avrebbe creato troppi problemi.
Del resto le alternative non erano molte. Cartiere del Garda doveva porre rimedio ai limiti di un impianto automatico ormai datato senza che da ciò ne derivassero più costi che benefici, e quella era l’unica strada percorribile. Zucchini, da buon ingegnere, mette in fila una dopo l’altra le varie ragioni che hanno fatto da cornice al progetto di revamping.
Puoi leggere l’intera Case History in questa pagina.
“Le componenti elettroniche erano ormai obsolete e la loro manutenzione o sostituzione con pezzi di ricambio richiedeva sempre più tempo. La probabilità di un guasto all’impianto era ormai arrivata a livelli eccessivi, così come quella di danneggiamento delle bobine dovuto alla scarsa precisione dell’impianto nelle operazioni di deposito e prelievo. In caso di stop improvvisi, i sistemi di diagnostica non consentivano di risalire alla fonte. L’impianto di raffreddamento e i comandi manuali non funzionavano più a dovere. Il sistema di supervisione era datato e a livello di visibilità il deposito era sostanzialmente inesistente”.
Insomma, tanti problemi che impattavano negativamente sulle prestazioni della linea e, per questa via, sull’intera performance aziendale.
ORGANIZZAZIONE SVIZZERA, CUORE ITALIANO
Stanti le premesse e considerando l’imperativo di Cartiere del Garda di ridurre drasticamente il numero di guasti e di migliorare la precisione, mantenendo almeno inalterate le performance dell’impianto, l’intervento è stato organizzato con meticolosa attenzione e pianificato secondo un dettagliato crono programma fatto di azioni puntualmente temporizzate ed incastrate una nell’altra come in un puzzle.
Tutto ha avuto inizio qualche mese prima dell’avvio del lavori con le attività di progettazione e di acquisto dei componenti.
Per prima cosa, però, un team di tecnici LCS è stato inviato sul posto per posizionare diversi sensori laser che, ad impianto in funzione, avrebbero ricostruito con esattezza l’intera mappa del magazzino con il posizionamento di ogni singola bobina.
Poi, nei giorni precedenti la data di avvio del progetto, le operazioni sono state ripassate una dopo l’altra insieme al personale che avrebbe lavorato sul campo.
Identicamente Demag faceva tutti i rilievi necessari alla sostituzione dei motori e dei riduttori predisponendo tutto quanto era necessario ad evitare “sorprese”. Infatti, la problematica di sostituire motori e riduttori con altri di marca e modello diversi poteva dare grossi problemi in merito agli ingombri ed agli staffaggi. Era quindi necessaria una serie meticolosa di rilievi e predisposizioni meccaniche.
Anche Cartiere del Garda ha avuto il suo bel daffare in quanto anch’essa, facendo parte della squadra di agosto, doveva effettuare tutte le predisposizioni necessarie alla buona riuscita del progetto, ad esempio l’approvvigionamento del trasformatore 500v-400v da mettere a monte della blindo.
“A quel punto – sottolinea Zucchini – non potevamo sbagliare. Tutti erano al corrente di quello che dovevano fare e del tempo a loro disposizione. Soltanto così potevamo infatti ridurre i tempi morti ed essere certi che, salvo imprevisti, avremmo rispettato il programma e la scadenza finale”.
Risultato che poi, alla fine, è stato raggiunto non senza difficoltà.
201202-IlGiornaledellaLogistica
Leggi anche l’approfondimento Il magazzino con puntamento laser, una scheda tecnica sulla Case History di Cartiere del Garda.