Colma - Nuovo magazzino automatico con sistema put to light
- Home
- Case Studies
- COLMA – Nuovo magazzino automatico con sistema put to light
L'azienda e le necessità
Fondata negli anni ’90, l’azienda Colma Srl è attiva principalmente nel commercio dell’alluminio, accessori e complementi. Con un un’area di oltre 30.000 mq di depositi con merce pronta, è in grado di soddisfare tutte le richieste di profili e barre commerciali. Inoltre, con consegne garantite su tutto il territorio nazionale, l’azienda è diventata un centro di supporto logistico-tecnico per i serramentisti.
Uno dei punti di forza maggiori di Colma è la sua disponibilità a 360° di tutti i reparti di complemento per il serramento: taglio e piega lamiera, curvatura, progettazione, etc. Tale vicinanza ai clienti viene garantita grazie a rapidità, puntualità e precisione nell’evasione degli ordini. Pertanto, la necessità di offrire un servizio sempre più impeccabile ai propri clienti, ha spinto l’azienda verso le soluzioni LCS. In tal modo Colma è riuscita a trarre vantaggio dall’impiego di una proprietà a Teverola (CE), nella quale è stato possibile ingegnerizzare un prestante magazzino automatico ed implementare un innovativo sistema di picking per permettere una maggiore velocità e precisione nel completamento degli ordini.
Il progetto realizzato
La soluzione pensata per il Cliente è stata realizzata all’interno di un capannone preesistente e di proprietà. A seguito delle analisi effettuate da LCS è stato possibile implementare un magazzino automatico pallet con postazioni adibite al picking e smistamento ordini attraverso un sistema put-to-light. L’impianto gestisce 8 tipologie di UdC diverse (4UdC con la stessa base 800×1200 ma di altezze differenti e 4UdC con una base 1120×1200 ma di altezze differenti) ed è in grado di soddisfare i seguenti flussi logistici: 90UdC in ingresso e 90UdC in uscita all’ora (180 UdC orarie totali).
All’interno del magazzino automatico sono presenti accessori di serramenti, come cerniere, maniglie, guarnizioni, serrature ecc., che vengono stoccati su 4 livelli, sia a singola che a doppia profondità in funzione dell’altezza UdC. L’intero impianto è composto da 3 corridoi serviti da 3 trasloelevatori, collegati a loro volta alle 3 baie di carico e di picking attraverso una navetta rettilinea doppia che smista i pallet sulla base della destinazione.
Gli ingressi e le uscite sono previsti esclusivamente sulla prima Baia, in cui i pallet vengono caricati e scaricati tramite carrello operatore. In tale baia è previsto il controllo sagoma in ingresso, che in caso di anomalia dispone il pallet nuovamente all’operatore. Allo stesso modo, in caso di peso fuori standard, il sistema non accetta il pallet e l’UdC torna all’operatore. Pur rispettando le altezze e le dimensioni, in caso di base pallet non utilizzabile per eventuali irregolarità, l’UdC può essere caricata su un pallet schiavo 1120×1200. L’impianto è infatti dotato di un magazzino pallet vuoti (capacità 13 pallet), che può essere alimentato automaticamente da pile pallet precedentemente inserite, oppure introdotti al bisogno.
Il picking viene effettuato sulle 3 Baie in cui i tre operatori incaricati hanno delle liste prelievo che includono sia ordini esterni che ordini a banco; questi ultimi si riferiscono ad ordini provenienti dall’edificio adiacente in cui si trova il negozio di Colma. Gli ordini a banco hanno sempre la precedenza rispetto a quelli esterni; infatti, nel caso in cui arrivi un ordine di questo tipo, la baia o le baie preposte, terminata l’operazione di picking in essere, interrompono la lista di prelievo per evaderlo il più rapidamente possibile. Sia le righe d’ordine per gli esterni che gli ordini a banco vengono quindi evasi sulle baie di picking, ove il prelievo viene effettuato in una postazione corredata da una tavola elevatrice per gestire l’ergonomia delle operazioni.
A fianco di ogni operatore è predisposto un sistema di put-to-light, che guida l’operatore e ottimizza le operazioni di deposito del materiale mediante display luminosi installati su uno scaffale a 2 livelli, con capacità massima di 8 liste da gestire contemporaneamente per operatore, di cui 2 mantenute vuote per eventuali richieste di ordini a banco. Ricevuto il pallet contenente il materiale di uno o più ordini, l’operatore può smistare gli articoli prelevati su uno o più ordini aperti in quel momento. Il sistema infatti indica a display la quantità e la tipologia di prodotto da prelevare e da destinare alle richieste in essere.
Ciò che permette la supervisione ed il controllo dell’impianto è la soluzione LCS LogiCon che si interfaccia direttamente con il sistema WMS di gestione del magazzino LogiWare di LCS. Quest’ultimo permette la gestione fisica e logica dei magazzini automatici e manuali. In particolare, LogiWare si occupa delle attività gestionali e si interfaccia sia con il sistema LogiCon per controllo della movimentazione sia con l’ERP aziendale del Cliente.
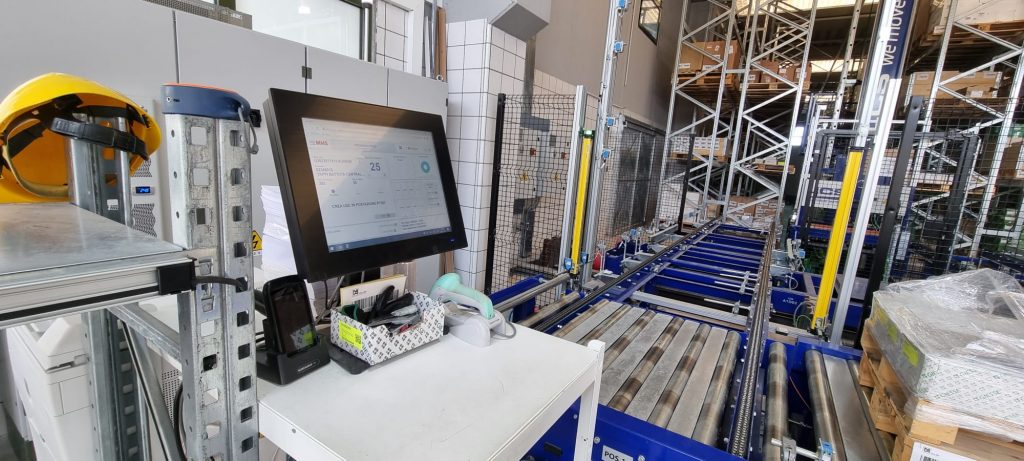
Benefici ottenuti
L’implementazione di tale soluzione ha permesso a Colma di ottenere numerosi vantaggi tra cui:
- Recupero e valorizzazione di un edificio di proprietà inattivo
- Incremento capacità di stoccaggio
- Ergonomia delle operazioni
- Velocità e precisione nella fase di preparazione ordini
- Gestione delle priorità per le liste ordini
- Ottimizzazione della logistica interna
- Maggiore soddisfazione dei clienti con riduzione dei lead time nell’evasione degli ordini