Colma - New automatic warehouse with a put-to-light system
- Home
- Case Studies
- COLMA – New automatic warehouse tih a put-to-light system
The company and the needs
Colma Srl, established in the 1990s, is primarily involved in the trade of aluminum, accessories, and components. With an area of over 30.000 square meters of ready-to-ship goods, it can meet all requests for commercial profiles and bars. With guaranteed deliveries throughout the national territory, the company has become a logistic-technical support center for joiners.
One of Colma’s greatest strengths is its 360-degree availability of all complementary components for windows and doors frame: sheet metal cutting and bending, curving, design, etc. This proximity to customers is guaranteed by the rapidity, punctuality, and accuracy in order processing. Therefore, the need to offer an ever more impeccable service to its customers has led the company towards LCS solutions. In this way, Colma was able to benefit from the use of a property in Teverola (CE), where it was possible to engineer a high-performance automated warehouse and implement an innovative picking system to allow greater speed and accuracy in order fulfilment.
The realized project
The solution designed for the customer was implemented inside an existing and owned warehouse. Following the analysis carried out by LCS, it was possible to implement an automatic pallet warehouse with picking and order sorting stations using a put-to-light system. The plant manages 8 different types of loading units (4 with the same base 800×1200 but different heights and 4 with a base 1120×1200 but different heights) and is capable of satisfying the following logistics flows: 90 load units in and 90 load units out per hour (total 180 load units hourly).
Within the automated warehouse are window and door accessories, such as hinges, handles, seals, locks, etc., stored on 4 levels, both single and double depth, depending on the loading unit height. The entire plant consists of 3 aisles served by 3 stacker cranes, connected in turn to the 3 loading and picking bays through a double linear shuttle that sorts the pallets according to destination.
Inputs and outputs are only available on the first bay, where pallets are loaded and unloaded by an operator cart. In this bay, there is a shape control on entrance, which in case of anomaly returns the pallet to the operator. Similarly, in the event of an out-of-standard weight, the system does not accept the pallet and the loading unit returns to the operator. While respecting the heights and dimensions, in the case of a pallet base that cannot be used due to any irregularity, the loading unit can be loaded onto a 1120×1200 slave pallet. The system is in fact equipped with an empty pallet magazine (capacity 13 pallets), which can be automatically fed from previously inserted pallet piles, or introduced as required.
Picking is carried out on the 3 bays where the three operators in charge have picking lists that include both external orders and over-the-counter orders; the latter refer to orders from the adjacent building where the Colma shop is located. Over-the-counter orders always take priority over external orders; in fact, in the event that such an order arrives, the bay or bays in charge, having completed the picking operation in progress, interrupt the picking list in order to process it as quickly as possible. Both outside order lines and counter orders are then dispatched to the picking bays, where picking is carried out at a station equipped with a lift table to manage the ergonomics of operations.
Next to each operator there is a put-to-light system, which guides the operator and optimises the material deposit operations by means of luminous displays installed on a 2-level shelf, with a maximum capacity of 8 lists to be managed simultaneously per operator, 2 of which are kept empty for possible requests for counter orders. Having received the pallet containing the material of one or more orders, the operator can sort the picked articles onto one or more orders open at that moment. The system in fact indicates on the display the quantity and type of product to be picked and to be assigned to the outstanding requests.
What enables the supervision and control of the system is the LCS LogiCon solution that interfaces directly with the LCS LogiWare warehouse management WMS system. The latter allows the physical and logical management of automatic and manual warehouses. In particular, LogiWare takes care of the management activities and interfaces both with the LogiCon system for handling control and with the customer’s company ERP.
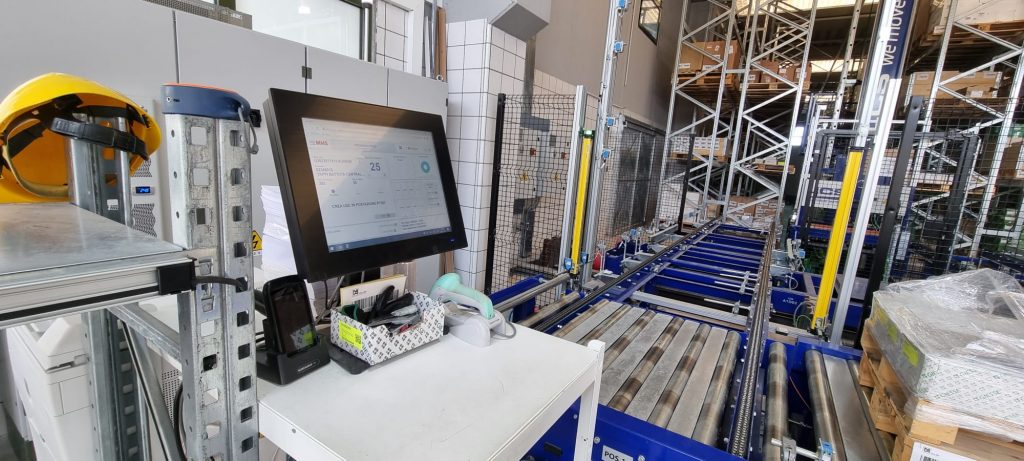
Benefits achieved
The implementation of this solution has enabled Colma to achieve numerous benefits including:
- Recovery and valorization of an inactive property building
- Increased storage capacity
- Ergonomics of operations
- Speed and accuracy in the order preparation phase
- Priority management for order lists
- Optimization of internal logistics
- Increased customer satisfaction with reduced lead times in order processing