Camar – The new Hi-Tech automatic warehouse
- Home
- Case Studies
- CAMAR – The new hi-tech automatic warehouse
The constant commitment of an industrial company is customer satisfaction that starts with efficient management and speed of execution of the warehouse. LCS has created an automatic customer satisfaction proof warehouse for Camar.
The company and the needs:
Camar is a world leader in the design and production of technical fittings for the furniture industry. The company was established in 1960 and is located in the centre of Brianza, the traditional furniture district in North Italy. Sensitive to the demands of the market, Camar offer many possibilities for customising products on a large part of their range. A skilled consulting team, dedicated to customer service, is ready to help with any requirement.
Camar decides to revisit its storage facilities and entrusts LCS with the task of studying the best solution to optimize the flow of intralogistics. At the headquarter in Figino Serenza (CO), the storage area was divided into different areas that did not allow a smooth connection both in entrance, to the production, and in exit of the finished product.
LCS’s task was therefore to modernize the existing storage and handling system (1997). With a more structured and automated flow, an appropriate speeding up of the movements between production departments and warehouse would have been achieved, resulting in an increase in customer satisfaction thanks to faster and more precise deliveries.
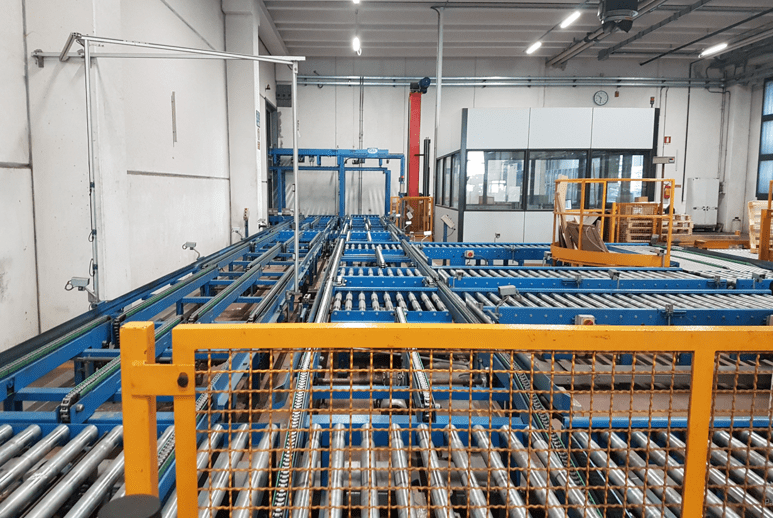
The implemented solution
The LCS project envisaged the revamping of the existing warehouse in very short times (one month) which were maintained.
Specifically, LCS intervened with a retrofit operation on the electromechanical part of the three existing stacker cranes operating in simple depth on shelves of 15 meters in height for a total storage of 3,800 pallets. Furthermore, in order increase its performance, the header shuttle was replaced for the connection with the new automatic warehouse.
The new solution is governed by a highly customized LCS proprietary software package based on customer needs. LCS has completely renewed the software PLC of automation, of the WCS for plant supervision and of the WMS for warehouse management. The solution was extensively tested before implementation to ensure the short time for the restart of the plant, which operates on three floors.
In addition to the revamping of the existing warehouse, LCS took care of the planning that included the increase in storage capacity of the warehouse.
A new self-supporting automatic warehouse was built with 4 stacker cranes (H = 17 m for 6200 loading units). An elevated bridge was built to connect the new warehouse to the existing one and on this bridge operates the new shuttle installed during the revamping phase of the existing warehouse that connects the heads of the two warehouses operates. The conveyor system serving the new production departments was expanded and the new automation, supervision and warehouse management software was implemented.
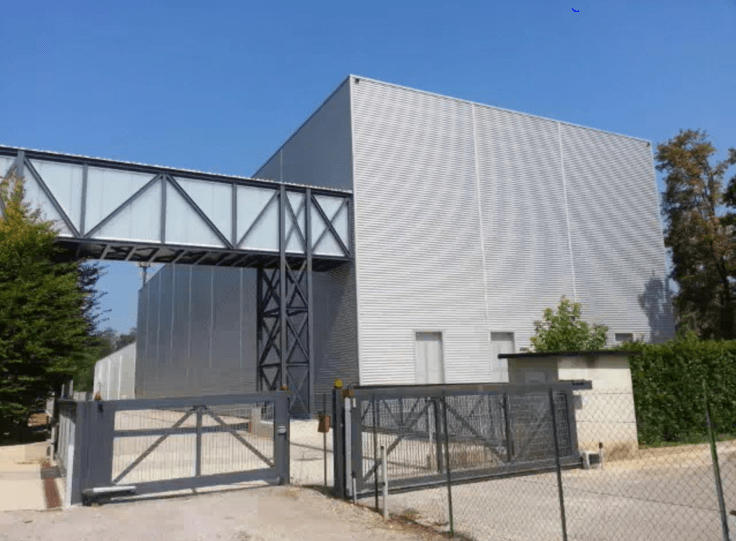
Benefits
LCS’s task was to design a system that centralized the materials in a single warehouse to achieve maximum synergy between the various production departments without neglecting the timeliness and accuracy of shipments.
In particular:
- No loss of turnover during the important retrofit intervention
- Greater efficiency in production
- Intralogistic optimization
- Increase of storage capacity
- Reduction of the capital employed in the production cycle
- Greater customer satisfaction with reduced lead times in order fulfillment
The revamping combined with the expansion of the Camar warehouse was made possible thanks to the great collaboration between the client and the supplier, pursuing objectives based on common values: customer satisfaction and a passion for extreme quality.
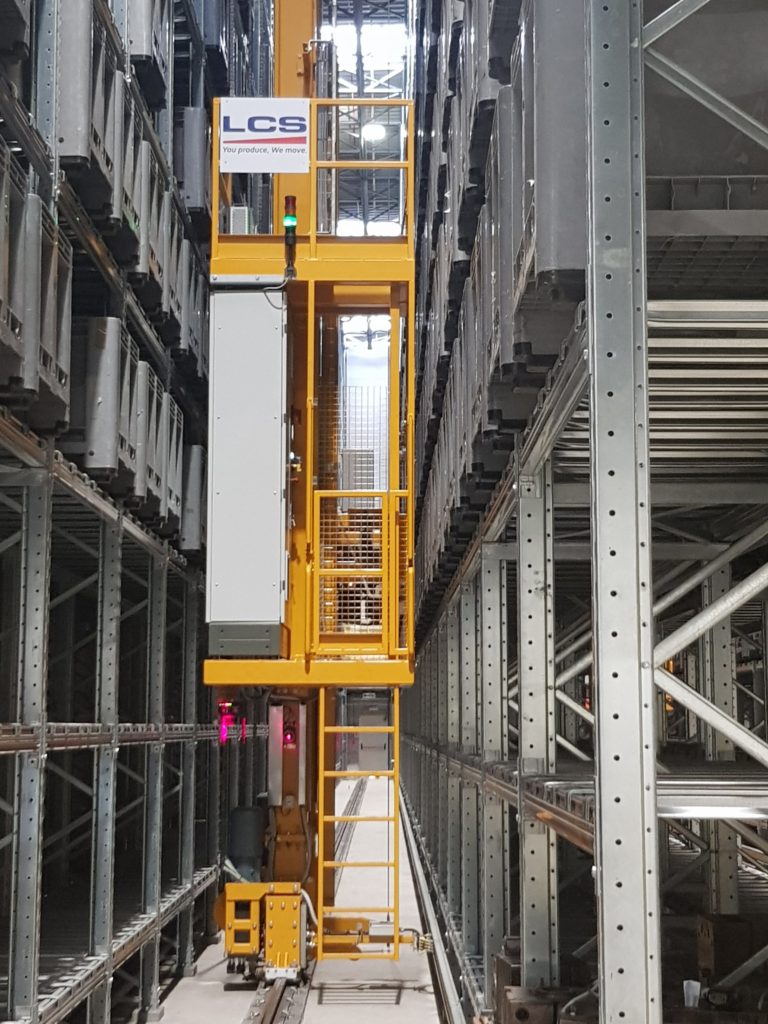