La Growermetal, storica azienda di Calco (LC), produce rondelle piane, elastiche di sicurezza e molle per armamento ferroviario. La produzione dell’azienda è destinata per quasi l’80% all’esportazione in tutto il mondo.
L’azienda lavora 16mila tonnellate di materie prime dalle quali genera 4 miliardi di pezzi tranciati da nastri e 320 milioni di pezzi formati da filo. Una simile produzione esige una logistica robusta. L’azienda si affidava, fino a poco tempo fa, ad un magazzino manuale adiacente alla zona produttiva, ma con tutte le limitazioni che dava la gestione manuale del processo.
Opta dunque per un nuovo magazzino automatico. Puoi leggere la case history completa in questa pagina.
“L’evoluzione compiuta dalla nostra azienda, con il conseguente aumento delle complessità operative”, spiega Ernesto Cattaneo, AD di Growermetal, figlio primogenito del fondatore della società Virginio Cattaneo, “richiedeva ormai nuovi spazi operativi per la supply chain. Ci eravamo resi conto che negli ultimi anni l’impresa aveva continuato a crescere in tutti i suoi reparti produttivi, mentre il magazzino del prodotto finito era rimasto fermo, diventando un “collo di bottiglia”. Una dettagliata analisi di tutte le possibili soluzioni del problema ci ha fatto rapidamente capire che la costruzione di un magazzino automatico sarebbe stata la risposta più adeguata per l’ottimizzazione della fase fi nale del nostro ciclo produttivo.”
Ernesto Cattaneo, AD di Growermetal
Con questa scelta la Growermetal persegue alcuni obiettivi strategici. Il magazzino automatico riallinea il livello tecnologico del reparto di logistica a quello raggiunto dal resto dell’azienda, permettendo di conservare la leadership nel settore.
Un secondo importante obiettivo è rappresentato dalla sostenibilità. In termini di superficie edificata, una costruzione verticale in un contesto territoriale che non consente particolari espansioni orizzontali, rappresenta una soluzione lungimirante e di grande sostenibilità, anche economica.
Il magazzino autoportante misura 20 m di altezza per un totale di 11.000 locazioni e si estende su una superficie di 900 mq.
Ad LCS viene affidata l’intera progettazione del sistema integrato di magazzino. Mediamente l’impianto lavora ad un ritmo di oltre 800 missioni giornaliere, su un unico turno di 8 ore. Il magazzino automatico è integrato in un sistema che innesta innovazione lungo ogni fase della catena logistica, dal picking, al packaging fino ad arrivare alla spedizione.
Direttamente dai reparti produttivi la merce viene caricata nelle due baie di ingresso. Qui, viene presa in carico da uno dei 4 LGV (Laser Guided Vehicle) e convogliata al magazzino automatico. I veicoli automatici a guida Laser LGV sono un sistema molto versatile che consente di modificare i percorsi dell’impianto in maniera facile e veloce.
“La scelta di utilizzare degli LGV al posto di un sistema di rulliere fi sse”, spiega Gianfranco Silipigni, AD di LCS, “è stata dettata dalla volontà di ottenere la massima flessibilità, evitando di ingabbiare la supply chain in strutture troppo rigide, e ottenere un sistema modulare e scalabile che, potesse evolvere al mutare delle esigenze. In caso di aumento di necessità, infatti, l’attività può essere intensificata con l’inserimento di un’ulteriore macchina, senza dover modificare l’infrastruttura già esistente”.
Gianfranco Silipigni, AD di LCS
Agli LGV viene affi dato anche il prelievo dei pallet estratti dalle 4 baie di scarico dei trasloelevatori secondo le missioni pianificate dal software di Warehouse Management System di LCS e di veicolarli fino all’area di picking. Qui, gli operatori possono effettuare il prelievo e preparare la merce per la spedizione agevolati da un’automazione ergonomica e studiata per garantire il giusto mix tra comfort e produttività, a partire dal sistema di regolazione dell’altezza del pallet, che permette al pickerista di variare l’altezza del piano di lavoro.
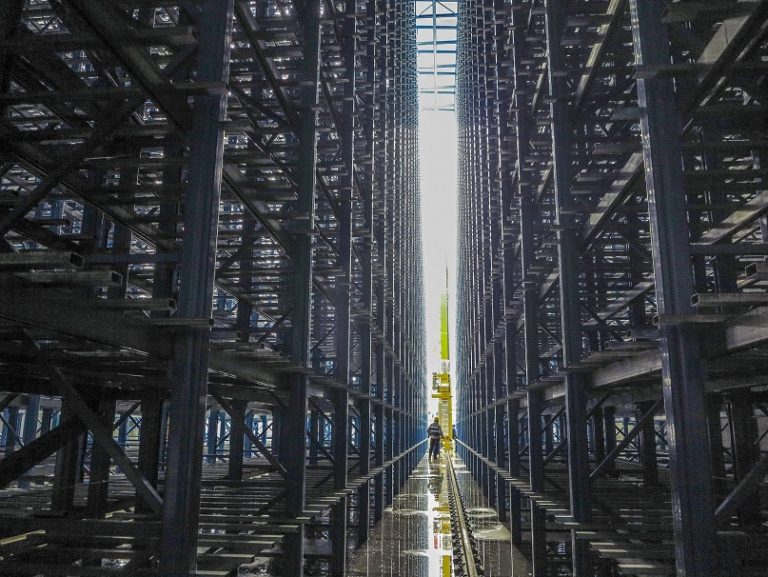
L’impianto è stato dimensionato sia a livello di spazi sia di prestazioni per supportare le future crescite aziendali. “Quando abbiamo inaugurato l’impianto, la crisi mordeva ancora, ma conoscendo la nostra realtà, sapevamo che saremmo riusciti a conseguire una positiva crescita.”
“Gli investimenti fatti sono benzina per ulteriori futuri sviluppi. Crediamo in questo progetto e guardiamo al futuro con concreto ottimismo. Vogliamo essere ben equipaggiati per cogliere tutte le opportunità che si possono presentare.” spiega Cattaneo.
Il nuovo impianto ha portato sin da subito concreti benefici. La razionalizzazione degli spazi ha garantito una maggior capacità di far fronte all’aumento dei volumi movimentati. L’integrazione dell’automazione ha portato a una revisione e standardizzazione dei processi che consente l’aumento della produttività e l’aumento della flessibilità.
L’ergonomia delle soluzioni adottate, ha migliorato sicurezza, comfort e produttività. Infine l’ottimizzazione dell’interazione uomo-macchina ha assicurato una migliore tracciabilità e un ulteriore abbattimento degli errori in fase di spedizione.
Articolo pubblicato su Il Sole 24 Ore