Camar – Il nuovo magazzino automatico Hi-Tech
- Home
- Case Studies
- CAMAR – Il nuovo magazzino automatico Hi-Tech
L’impegno costante di un’impresa industriale è la soddisfazione del cliente che parte da una efficiente gestione e velocità di esecuzione del magazzino. LCS ha realizzato per Camar un magazzino automatico a prova di “customer satisfaction”.
L’azienda e le necessità:
Camar, fondata nel 1960 e strategicamente posizionata al centro del distretto brianzolo del mobile e dell’arredamento, è attualmente leader mondiale nella progettazione e nella produzione di articoli tecnici per l’industria del mobile con prodotti innovativi e di altissima qualità, che spaziano dai livellatori, piedini, supporti per pensili, mensole e basi fino alle gambe per tavoli.
Attenta alle esigenze espresse dal mercato, Camar offre, su gran parte della propria produzione, diversificate possibilità di personalizzazione e l’attività di consulenza di un team preparato e affiatato, da sempre, al servizio del cliente.
Camar decide di rivisitare le proprie strutture di stoccaggio ed affida a LCS il compito di studiare la soluzione migliore per ottimizzare il flusso della intralogistica. Nella sede centrale di Figino Serenza (CO) l’area di stoccaggio era suddivisa in zone diverse che non consentivano una fluida connessione sia in ingresso, verso la produzione, sia in uscita del prodotto finito.
Il compito di LCS è stato quindi quello di ammodernare l’impianto di stoccaggio e movimentazione esistente (1997). Con un flusso più strutturato e automatizzato si sarebbe raggiunta una opportuna velocizzazione delle movimentazioni tra reparti produttivi e magazzino, pervenendo all’incremento della soddisfazione del cliente grazie a consegne più rapide e precise.
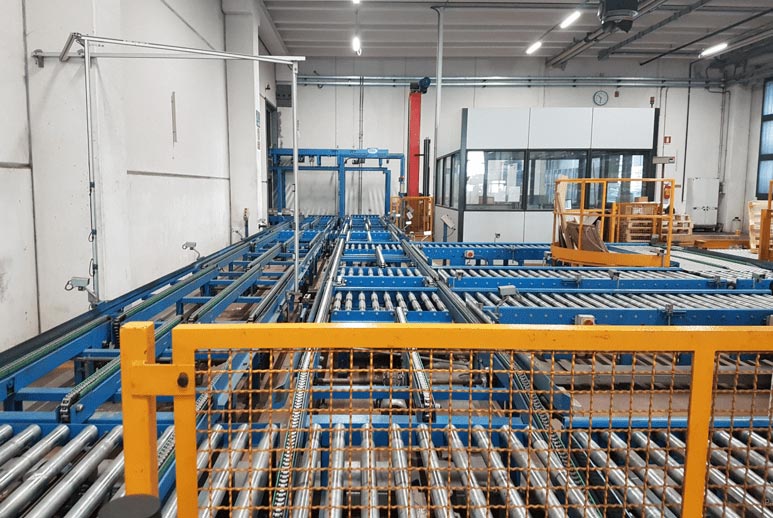
Il progetto realizzato
La progettualità di LCS prevedeva per il revamping del magazzino esistente in tempi molti stretti (un mese) che sono stati mantenuti.
Nello specifico LCS è intervenuta con un’operazione di retrofit sulla parte elettromeccanica dei tre trasloelevatori esistenti ed operanti in semplice profondità su scaffali di 15 metri in altezza per uno stoccaggio complessivo di 3.800 posti pallet. Inoltre, per poter incrementare ulteriormente le proprie performance, è stata sostituita la navetta di testata per il collegamento con il nuovo magazzino automatico.
La nuova soluzione è governata da un pacchetto software proprietario LCS altamente personalizzato in base alle esigenze del cliente. LCS ha completamente rinnovato il software dei PLC di automazione, del WCS per la supervisione degli impianti e del WMS per la gestione del magazzino. La soluzione è stata ampiamente testata prima della implementazione per garantire i tempi ristretti per la ripartenza dell’impianto, che opera su tre piani.
- Primo piano: ingresso merci (fornitori/produzione/rientri da picking) con identificazione e controllo dimensionale delle Udc; uscita Udc destinate a reparti produttivi; uscita Udc da magazzino destinate a spedizione e picking
- Secondo piano: ingresso pallet in arrivo dal piano terra tramite elevatore
- Terzo piano: uscita Udc verso reparti produttivi e rientro a magazzino di Udc di prodotto finito
Oltre al revamping del magazzino esistente, LCS si è occupata della progettualità che prevedeva l’aumento della capacità di stoccaggio del magazzino.
E’ stato realizzato nuovo magazzino automatico autoportante con 4 trasloelevatori H=17 m per 6200 posti Udc. Un bridge sopraelevato è stato costruito per collegare il nuovo magazzino al magazzino esistente e su questo ponte opera la nuova navetta installata durante la fase di revamping del magazzino esistente che collega le testate dei due magazzini. E’ stato ampliato l’impianto di convogliamento a servizio dei nuovi reparti produttivi e implementato il nuovo software di automazione, supervisione e gestione magazzino.
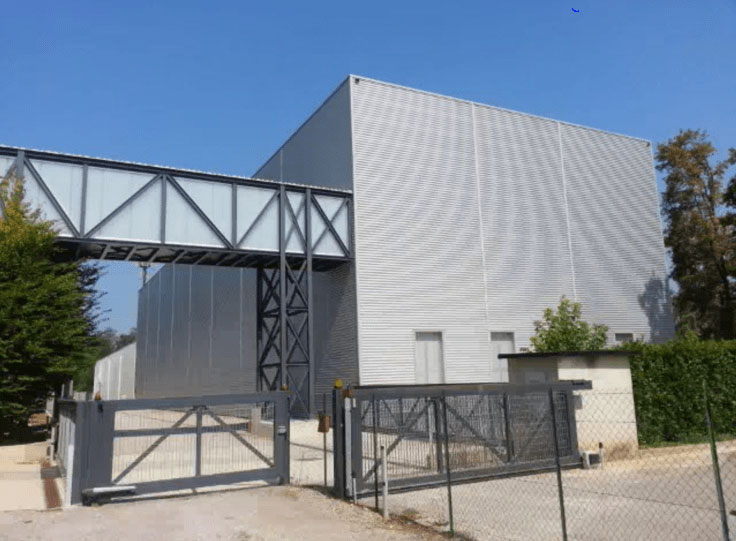
Benefici ottenuti
Il compito di LCS è stato quello di progettare un impianto che centralizzasse in un unico magazzino i materiali per ottenere la massima sinergia tra i vari reparti di produzione senza tralasciare la tempestività e l’accuratezza delle spedizioni.
Nello specifico:
- Nessuna perdita di fatturato durante l’importante intervento di retrofit
- Maggiore efficienza in produzione
- Ottimizzazione logistica interna
- Incremento capacità di stoccaggio
- Riduzione del capitale impegnato nel ciclo produttivo
- Maggiore soddisfazione dei clienti con riduzione dei lead time nell’evasione degli ordini
Il revamping unito all’ampliamento del magazzino di Camar è stato possibile grazie alla grande collaborazione tra committente e fornitore perseguendo obiettivi basati su comuni valori: la soddisfazione del cliente e la passione per l’estrema qualità.
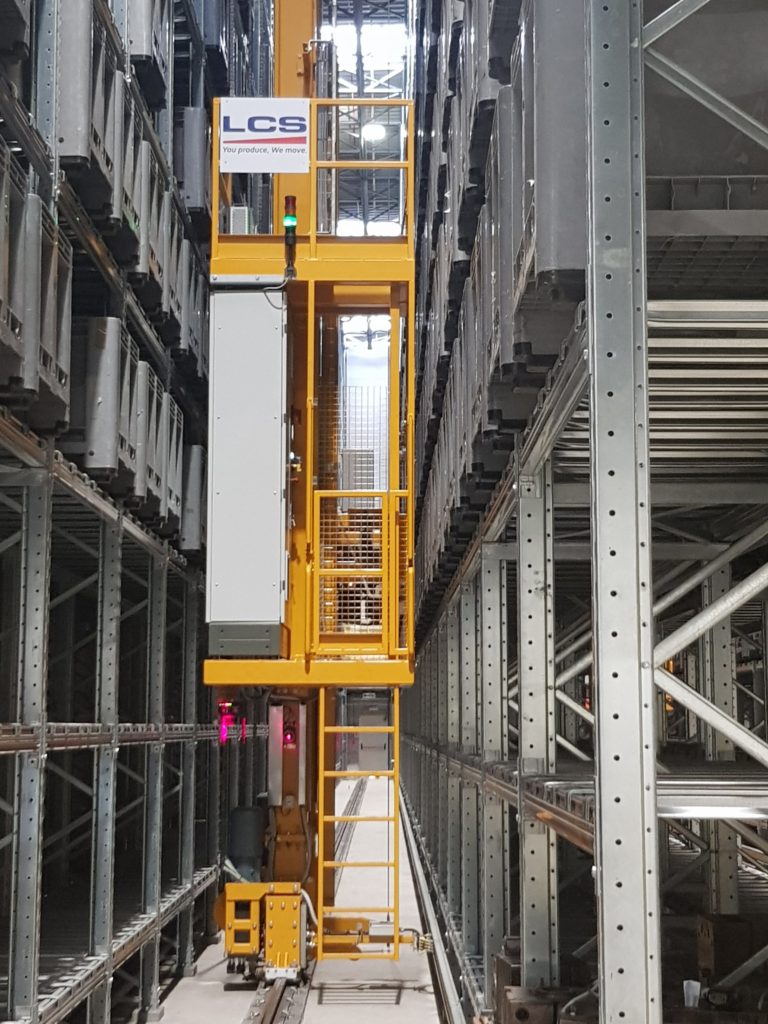