MARCOLIN - Sistema automatico di movimentazione per occhiali
- Home
- Case Studies
- MARCOLIN – Automatic handling system for glasses
LCS creates an end-of-line system for Marcolin for the management and packaging of packages for shipment. Efficiency, optimization of operations and high performance are just some of the benefits obtained.
L'azienda e le necessità
The company and the needs:
With over 1700 employees, 4 logistics centers and 14 branches around the world, Marcolin has been creating, manufacturing and distributing sunglasses and eyeglasses for well-known brands for 60 years. The success of the company, a leading reality for the eyewear sector, derives from the combination of the Italian artisan tradition with a particular ability to intercept and make its own the evolutions of the fashion world.
Thanks to this the company has established itself internationally and continues to extend and include a large number of brands. To date names such as Tom Ford, Guess, adidas Sport, adidas Originals, Bally, Moncler, Max Mara and many others have chosen Marcolin.
Marcolin’s goal, within the Longarone (BL) site, was to implement an automatic system capable of automating all those operations that were carried out manually by the operators. This project allowed not only to automate, reorganize and speed up operational flows, but also ensured the traceability of items and the elimination of errors due to manual management.
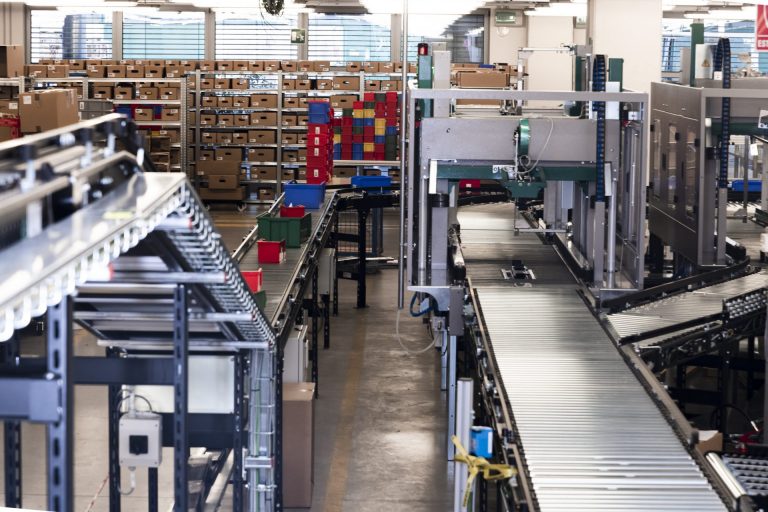
Il progetto realizzato
The realizsed project:
The project developed and implemented by LCS includes an end-of-line system for the management and packaging of packages for shipment.
The warehouse operators pick up the glasses from the shelf warehouse located on the upper floor. The collected glasses are placed in single-order or multi-order boxes with barcode.
Through a high-performance continuous elevator, the boxes are transferred to the lower floor at a height of 800 mm from the ground, to then be sorted on the 12 packaging bays present.
The operator in this station manually reads the box code using a barcode reading device and the type of box that he will use is displayed on the PC at his disposal, together with the delivery lines with details on the quantities.
Once the barcode label has been printed and applied to the box that associates it with the order, the lights of the pick to light system turned on behind the operator in correspondence with the “case” items to be withdrawn. Once the cases have been picked up and identified, the various codes are read, as is the reading of the code of the glasses present in the picking box coming from the picking, and then everything is inserted into the shipping package.
At the end of the packing phase, the package is processed manually through the exit belt.
Delivery customization
Some deliveries require product customization.
– On days of medium-low productivity, the customizations are carried out directly in the packing bay.
– On days of high productivity, the involved packages are divided, based on the type of customization, into 4 customization bays.
Package closing and sorting:
The packages coming from the packing and personalization bays are conveyed towards the flap closing and taping area and the weight detection area. Those packages to which the invoice is applied on the outside are evacuated through a conveyor, while the re-entry of them on the main roller conveyor is performed manually by the operator.
At this point the packages continue towards the shipping label printer, whose label is positioned on the top, and sorted into the 15 outings for shipping, while any unread packages are ejected into a dedicated exit.
Software
The functioning of the automatic system and autonomous tracking of the packages are guaranteed by the LCS LogiCON software, which has the task of controlling and supervising the entire system.
The plant is also equipped with LogiWare software, a system for the physical and logical management of automatic and traditional warehouses. Specifically, for the Marcolin project, this software is used for:
• Management of packing orders in the bays
• Management of the pick to light system
• Management of the stock related to the cases
• Management of the refilling request of the cases when under stock
• Management of label printing of shipping packages
The software interfaces with the LCS LogiTrasp PLC software system for handling control and with the customer’s SAP ERP.
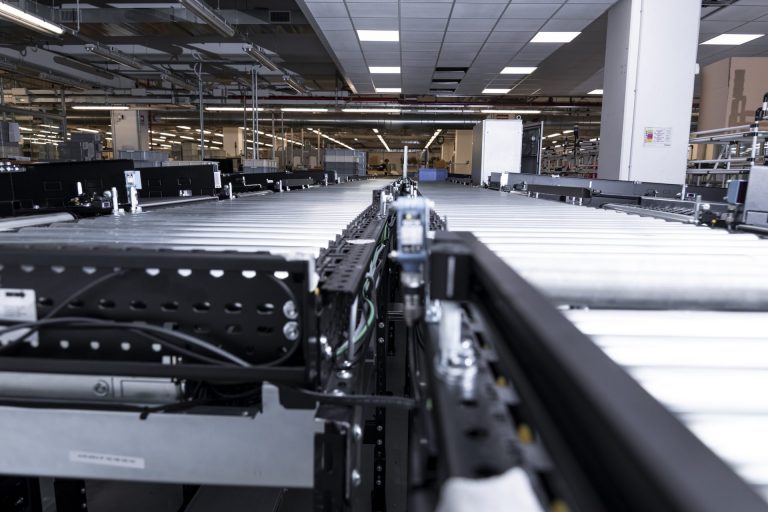
Benefici ottenuti
Obtained benefits:
The project carried out by LCS for Marcolin allowed to:
• Increase the efficiency of operational flows
• Automate all those processes that were previously carried out manually
• Eliminate errors due to manual management
• Obtain constant tracking and control of all items and processes.
• Optimize and relocate resources in a timely manner for each warehouse process
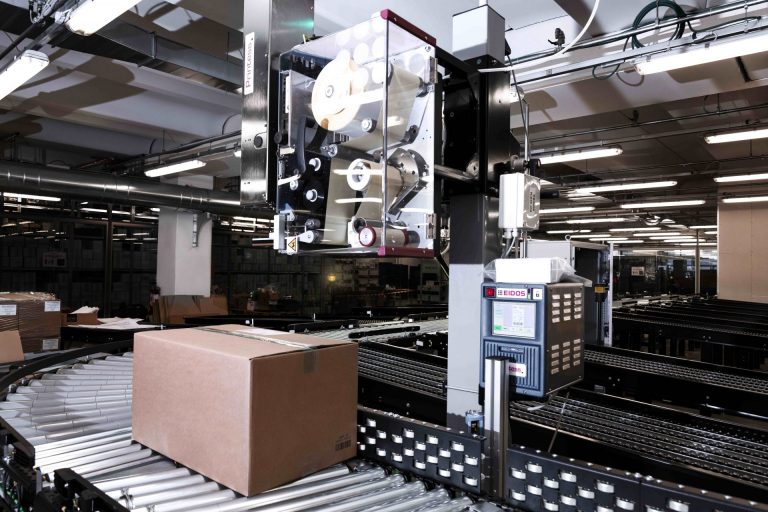