Bisio Progetti – La tecnologia 4.0 nella robotica mobile
- Home
- Case Studies
- BISIO PROGETTI – La tecnologia 4.0 nella robotica mobile
Il progetto LCS ha permesso l’integrazione di nuovi paradigmi 4.0 con l’obiettivo di ottimizzare efficienza e flessibilità garantendo continuità e sicurezza.
L’azienda e le necessità:
Bisio Progetti è un’azienda italiana che si occupa di stampi e lavorazione di materiale plastico conto terzi, con headquarter e sede produttiva ad Alessandria. Nel 1990 incorpora, a seguito di un’operazione di fusione, una società di stampaggio e lavorazione materie plastiche (R3 S.r.l) ed entra a far parte di un gruppo industriale molto noto in Italia e nel mondo, la Guala spa, operante nel settore delle chiusure di garanzia per liquori, dispenser per dentifrici e trigger.
L’azienda sviluppa negli anni un forte know how tecnologico nella ricerca e progettazione stampi di nuovi prodotti concepiti con tecnologie di materiali e forme che sanno incontrare le esigenze del mercato in continua evoluzione. Uno di questi è la produzione di capsule per caffè e altre bevande, che l’azienda riesce a soddisfare considerevolmente grazie ad un catalogo di capsule adatto alle richieste di ogni tipo di commessa.
La continua crescita delle richieste e l’esigenza di garantire la massima continuità delle operazioni, ha spinta l’azienda Bisio Progetti a ripensare al flusso di movimentazione intralogistico a 360° con una soluzione che permettesse di sfruttare le tecnologie 4.0, integrando hardware e software e aggiungendo valore al flusso produttivo nella piena continuità e sicurezza delle operazioni.
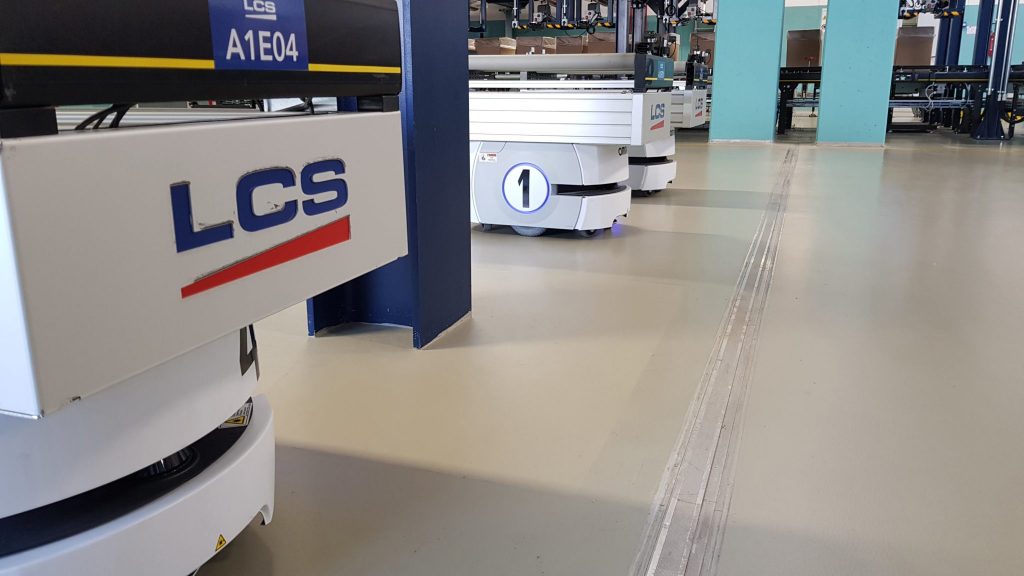
Il progetto realizzato
LCS, forte della sua partnership tecnologica con Omron, ha basato il progetto su robot mobili, detti AMR (Autonomous Mobile Robots). Tali robot rappresentano un avanzamento rispetto agli AGV tradizionali in quanto non richiedono integrazioni onerose al layout esistente ma navigano in autonomia, calcolando ogni volta il percorso più adatto per soddisfare le richieste di movimentazione in base alla loro posizione. Inoltre tale tecnologia sfrutta sensori laser e telecamere integrate per estrapolare dati in tempo reale sul percorso ed elaborarli grazie all’Intelligenza Artificiale per evitare ostacoli fissi o in movimento.
Per soddisfare una richiesta a picco di 210 scatole/h, è stata introdotta una flotta di 7 AMR. Ad ogni ciclo il robot alimenta con un cartone vuoto una macchina e carica un cartone pieno per poi trasportarlo all’area di chiusura. Hanno un’autonomia di 8h e dovendo garantire la massima disponibilità durante le operazioni, gestiscono autonomamente la loro ricarica: al raggiungimento della soglia di autonomia minima della batteria si recano verso l’area dedicata al cambio batteria, dove un operatore la sostituirà con una totalmente carica. I robot sono dotati di una rulliera automatizzata che permette il facile allineamento con le altre rulliere a valle delle macchine formatrici, riempitrici e al sistema per la chiusura automatica delle scatole.
Il sistema è coordinato dal software di supervisione LogiCon di LCS, che organizza la flotta dei robot e si interfaccia con il MES in modo da selezionare per ogni richiesta di movimentazione il robot più adatto per la sua movimentazione alle stazioni. Una volta terminato il riempimento di una scatola ad una stazione, viene mandata una richiesta al nodo centrale per richiamare una nuova richiesta da evadere. Il sistema raccoglie tutte le richieste dalle stazioni e le prioritizza in base alla coda di richieste da completare, alla velocità delle stazioni di riempimento e all’urgenza dell’ordine relativo alla richiesta. Una volta selezionata quella più adatta, il nodo centrale interroga tutti i robot per sapere il loro stato, ovvero se disponibili per effettuare una nuova missione o se ancor impegnati in quella precedente. La richiesta viene poi inviata al robot selezionato che calcola il percorso ottimale per evadere la richiesta. Al termine della richiesta il robot notifica il nodo centrale della missione completata. Il nodo centrale integra in modo efficiente la flotta dei robot con le richieste delle stazioni in tempo reale per garantire la massima continuità delle operazioni e ridurre gli errori.
Benefici ottenuti
Questo progetto di automazione è un esempio di movimentazione intelligente e flessibile che sfrutta tecnologie all’avanguardia in ottica industria 4.0.
- Riduzione dei tempi di fermo delle macchine per mancanza materiali ed errori di movimentazione, grazie all’elevata disponibilità ed affidabilità, alla precisione e ai ridotti tempi di movimentazione dei robot.
- Miglioramento della gestione delle aree produttive e la possibilità di impiegare operatori sulle attività che richiedono competenze umane (supervisione e miglioramento dei processi).
- Aumento di sicurezza nell’area del layout dedicata alla movimentazione grazie ai sistemi di movimentazione sicura.