GRUPPO RTS – Il magazzino multipiano per la gestione automatizzata dei ricambi auto
- Home
- Case Studies
- GRUPPO RTS – Il magazzino multipiano per la gestione automatizzata dei ricambi auto
L'azienda e le necessità
LCS realizza per il Gruppo RTS un sistema automatizzato di trasporto cassette per ricambi di automobili. Tale Gruppo, nasce dalla fusione di tre aziende: Ricauto, Top Car e Sarco. Ricauto SpA nasce nel 1973 e continua a crescere nel settore automobilistico, nello specifico distribuisce nell’area del Triveneto un’estesa gamma di componenti per auto (circa 90 mila articoli). TopCar S.r.l., nata nel 1980, opera anch’essa nel settore dei ricambi auto, distribuendo circa 75 mila riferimenti tra i più importanti marchi del panorama internazionale. Infine SARCO, la più longeva del gruppo, dai primi anni ‘60 opera nel settore ricambi, dapprima come produttore e poi come distributore, proponendosi come leader nelle linee silenziatori e catalizzatori, Termico e A/C, idraulica e Attritto, Tuning e Accessori.
Prima della fusione societaria, la gestione di tutti i ricambi avveniva in magazzini separati. L’obiettivo del cliente però era di convogliare tutti i prodotti, circa 100.000 codici, nello specifico quelli di Ricauto e SARCO, in un unico nuovo building. Inizialmente, all’interno dei vecchi magazzini, tutte le attività venivano effettuate manualmente dagli operatori (picking per ordine): dal prelievo del prodotto al trasporto, fino alla preparazione ordini per la spedizione. Tale meccanismo però creava non pochi problemi, soprattutto affaticava di molto gli operatori coinvolti con possibili infortuni sul lavoro. A fronte di ciò il cliente ha quindi deciso di automatizzare l’intero processo e di rivolgersi a LCS.
La soluzione realizzata è stata approfonditamente studiata e analizzata insieme ad un consulente e ad un fornitore di scaffali che il cliente aveva antecedentemente interpellato.
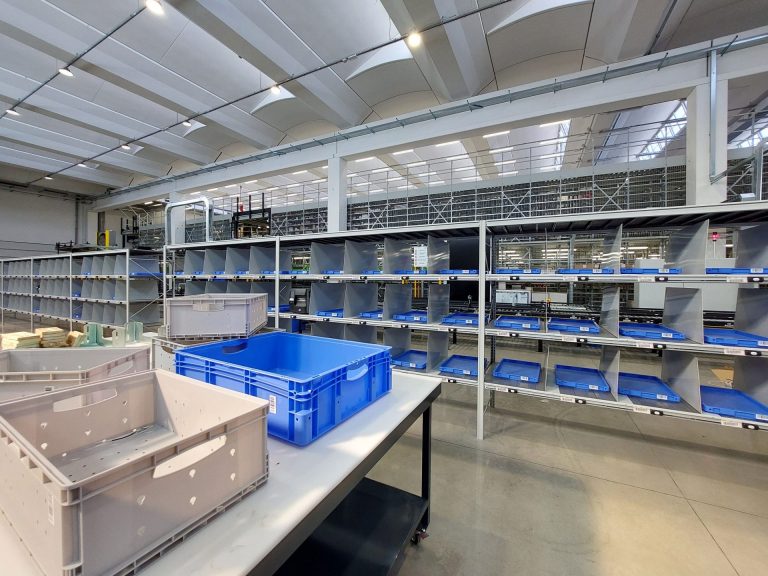
Le due fasi del progetto
Fase 1 – Linea di movimentazione cassette e area packing
Il nuovo building ha un’altezza complessiva di 9m ed è diviso su più piani: piano terra, primo e secondo piano. Ogni piano è suddiviso in 4 zone di lavoro con 4 operatori, in cui ogni operatore è responsabile del picking massivo all’interno della propria area di competenza.
Il singolo operatore, dopo aver eseguito le fasi di prelievo guidato dal WMS, deposita il prodotto all’interno di una delle due tipologie di cassette preposte, indicate dal WMS, ognuna con il proprio barcode di riconoscimento. Tali cassette sono presenti sulla propria linea di competenza, detta linea “verde”. L’automatizzazione del magazzino ha permesso pertanto di passare dalla modalità manuale di picking per singolo ordine, al picking massivo in base alla lista di prelievo segnalata dal software WMS. La linea “verde” ha un accumulo possibile di 4 cassette indipendentemente dalla tipologia di cassetta utilizzata: 600×400 oppure 800×600. Tale operazione si ripete per tutti e tre i piani all’interno delle quattro zone presenti, per un totale di 12 zone di picking massivo.
Un’esigenza fondamentale del progetto era poi quella di mantenere le vie di fuga libere in tutti i livelli. Per questo motivo le linee di trasporto sono state realizzate a quota 2220mm. Le linee di handling sopraelevate, che si trovano al piano terra, chiamate linee “arancioni”, sono collegate a tutte le linee verdi dei vari piani grazie alla presenza di 4 elevatori. Prima che la cassetta convogli verso la linea arancione tramite gli elevatori, viene effettuato il controllo dell’altezza; questo serve per evitare che quando la cassetta si trova in quota, si blocchi urtando contro il mezzanino posto sopra di essa. Pertanto se l’altezza non è conforme, la linea si blocca e l’operatore deve controllare e ripristinarne il contenuto.
Una volta depositate e controllate le cassette sulle linee “verdi” di competenza, queste convogliano verso le linee “arancioni”. Tali linee, provenienti dalle 4 zone, si uniscono in un’unica linea, a quota 3200mm prima di incontrare un discensore in continua, che porta le cassette a 700/800mm.
Le cassette, quindi, escono con al proprio interno tutti i prodotti misti, prelevati dagli operatori nelle 12 zone. Dopodiché grazie alla lettura del barcode posto su ognuna di esse, le cassette vengono convogliate verso le 6 uscite presenti, in funzione della corretta destinazione. Nelle varie uscite, si trovano diversi operatori che prelevano la cassetta e, guidati dal software, procedono alla ventilazione dell’ordine negli armadi, che presentano un sistema Put to light.
Nei periodi con minori ordini, ad esempio al pomeriggio, possono essere impiegati dai 2 ai 3 operatori, mentre nei periodi con un numero di ordini elevati, ad esempio alla mattina, possono essere presenti anche 5 o 6 pickeristi. Ognuno di essi deputato alla ventilazione degli ordini deve inserire le proprie credenziali nel sistema tramite username e password. Fatto questo passaggio, ad ognuno di essi viene associato un colore univoco che illumina le varie celle dell’armadio per evitare che si venga a creare confusione tra gli operatori durante il periodo di alta produzione.
L’armadio è composto da 210 celle aperte su due lati e ad ognuna di esse corrisponde a uno specifico cliente. All’interno di tali celle si trovano dei vassoi su cui vengono depositati gli articoli per la preparazione dell’ordine. Quando il sistema riconosce la completezza dell’ordine, si accende una luce verde dalla parte opposta dell’armadio in cui si trovano altri operatori, incaricati della preparazione degli ordini stessi. Ad ordine completo, la merce viene posizionata su un pallet destinato alla spedizione.
Una volta svuotata la cassetta, questa viene posizionata manualmente su una linea dedicata. Dopo aver effettuato la lettura del barcode e aver appurato che l’ordine è stato effettivamente completato, la cassetta viene convogliata verso uno dei due impilatori presenti, ognuno per la cassetta di competenza. Impilate 6 cassette, esse convergono verso un’uscita dedicata dalla quale vengono prelevate e depositate su un pallet per tornare ai vari piani per le nuove operazioni di picking, o trasportate verso la linea di refilling cassette chiamata “Linea Azzurra”.
Al piano terra vi sono poi due ulteriori uscite che possono oltrepassare la zona di ventilazione ordine:
- Uscita ordini monoriga: in questa linea possono arrivare tutti i colli o le cassette contenenti articoli destinati a ordini con un solo prodotto.
- Uscita ordini banco: all’interno del magazzino è presente un negozio in cui un cliente può ordinare direttamente gli articoli
Infine, a sud del magazzino, al piano terra, si trovano i materiali ingombranti che, data la loro dimensione, non vengono depositati all’interno delle due tipologie di cassette. Questi articoli oltrepassano la zona ventilazione ordini e vengono indirizzati alle postazioni di packing.
Fase 2 – Linea per il refilling
Sempre nella zona a sud del magazzino si trova l’area dedicata al refilling degli articoli nelle cassette. Come precedentemente descritto le cassette vuote impilate possono essere trasportate o su un pallet per tornare ai vari piani direttamente o sulla linea di refilling cassette chiamata “Linea Azzurra”.
Tutto il materiale in arrivo dall’esterno viene dapprima controllato e successivamente posizionato all’interno di una cassetta vuota che si trova sulla linea. La cassetta viene scannerizzata per l’associazione prodotto – cassetta e ne viene controllato il peso.
Se essa non è conforme viene scartata e indirizzata una linea dedicata, se invece risulta idonea allo stoccaggio procede verso un elevatore che la trasporta direttamente al secondo piano utilizzando una linea in quota. La cassetta poi procede fino a un altro lifter che la può scaricare al secondo piano o scendere ai piani sottostanti in base alla sua collocazione. L’operatore dedicato, grazie alla guida del WMS, preleva la cassetta e distribuisce i vari articoli nelle loro corrette postazioni.
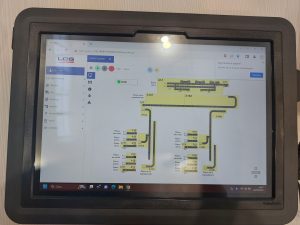
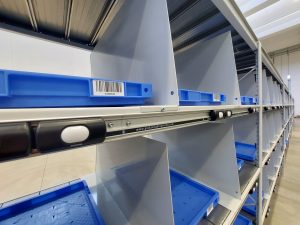
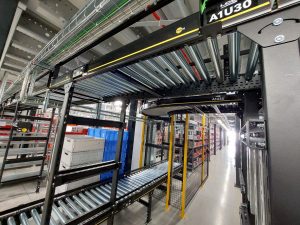
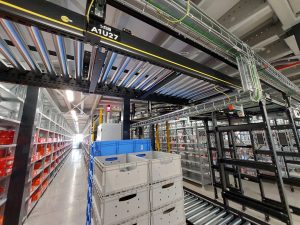
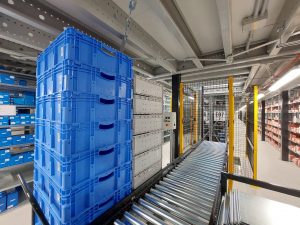
Il software
Dopo aver descritto nel dettaglio le varie fasi del progetto, rivolgiamo l’attenzione al sistema WMS, cuore dell’intero sistema. Il software di LCS, WMS LogiWare supporta la maggior parte delle attività svolte all’interno del magazzino. Tra le principali mansioni del software troviamo:
- Mappatura del magazzino con la gestione delle associazioni logiche tra posizioni e articoli
- Profilazione di tutti gli articoli presenti in magazzino
- Creazione liste di prelievo
- Creazione lista ordini
- Ubicazione del materiale a magazzino: per ciascuna UDC il WMS creerà delle liste di carico
ordinate per ubicazione. - Gestione della zona ventilazione ordini con sistema put-to-light
- Gestione delle spedizioni
- Interfaccia con sistema ERP aziendale
Il sistema LogiCon invece permette la supervisione ed il controllo dell’intero impianto automatico interfacciandosi con il sistema LogiWare.
I benefici ottenuti
I benefici e vantaggi derivati da tale soluzione sono stati fin da subito tangibili, nello specifico si è potuto osservare:
- Ottimizzazione dello spazio
- Velocizzazione delle operazioni
- Incremento capacità di stoccaggio
- Riduzione lead time nell’evasione degli ordini
- Predisposizione dell’impianto a futuri ampliamenti
- Attenzione all’ergonomia delle attività lavorative
- Incremento della sicurezza
Dati tecnici
- Altezza magazzino 9 metri suddiviso in tre piani: piano terra, primo piano e secondo piano
- Ogni piano suddiviso in 4 aree di competenza con 4 operatori distinti e altrettante postazioni di carico linea per ogni piano
- Trasporto cassette di due tipologie: 600×400 e 800×600, entrambe con altezza 220 (altezza prodotto max 400mm)
- Gestione di 100.000 codici prodotto presenti
- Passaggio da picking per ordine a picking massivo
- Impianto realizzato in due fasi:
- Fase 1: Linee Handling “verde”: l’operatore deposita la cassetta dopo il “batch picking”
- Fase 1: Linea Handling “arancione”: linea di trasporto cassette sopraelevata a quota 2220mm
- Fase 1: Linea di “ventilazione ordini”: linea di trasporto cassette con ventilazione ordini.
- Fase 1: Armadi con sistema “Put to light”.
- Fase 2: Linea Handling “azzurra”: linea di refilling cassette con arrivo dei nuovi materiali
- Potenzialità dell’impianto Fase 1: 500 cassette/h
- Potenzialità dell’impianto Fase 2: 150 cassette/h
- Presenza di nr. 8 discesori/elevatori.
- Area ventilazione ordini con sistema put-to-light e possibilità di gestione di 210 clienti
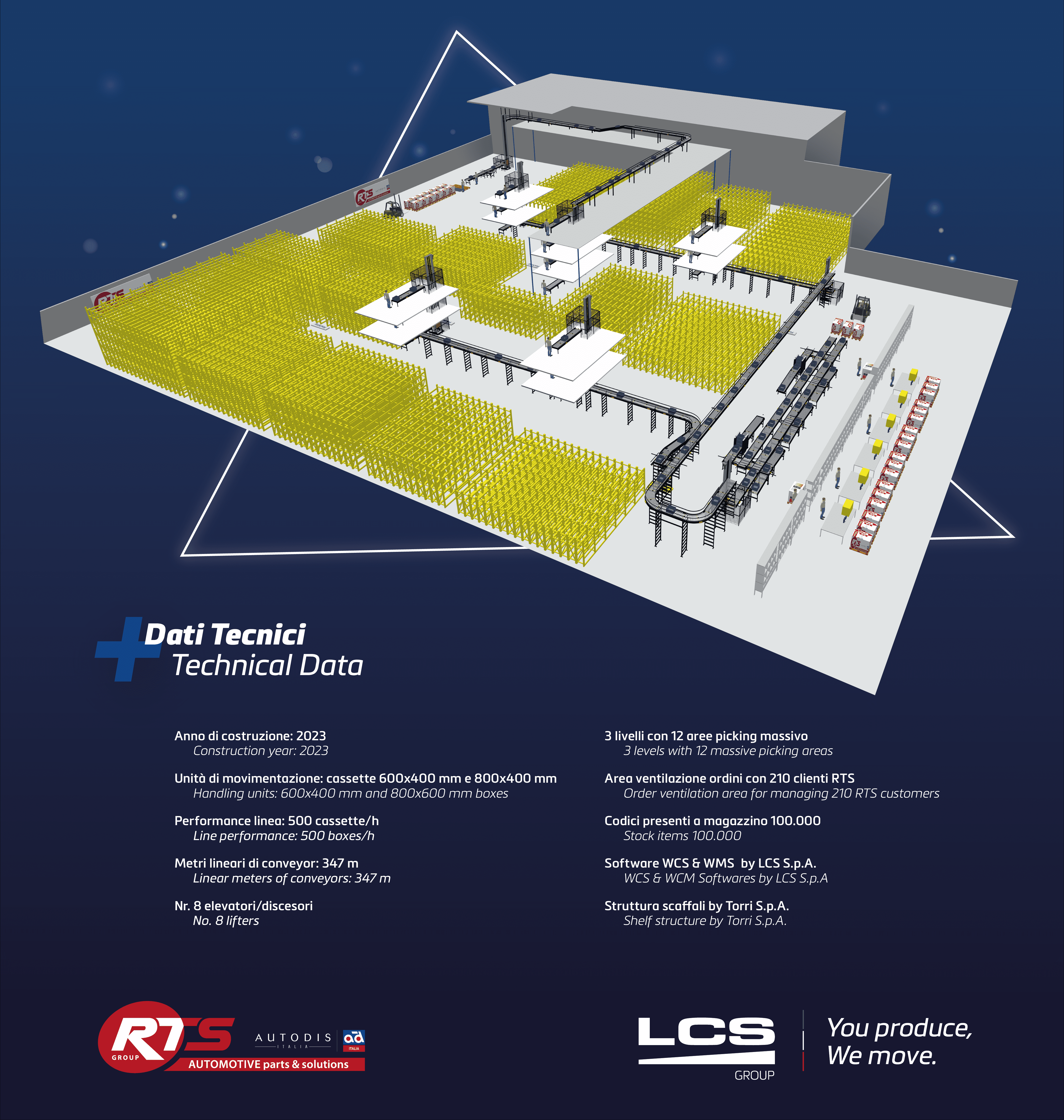