GRUPPO RTS – Il magazzino multipiano per la gestione automatizzata dei ricambi auto
- Home
- Case Studies
- RTS GROUP – The multi-level warehouse for automatic management of auto parts
The company and the needs:
LCS makes an automatic totes transport system for automobile spare parts for the RTS Group. This Group, was born from the merger of three companies: Ricauto, Top Car and Sarco. Ricauto S.p.A. was founded in 1973 and continues to grow in the automotive sector, specifically distributing in the Triveneto area an extensive range of car parts (about 90 thousand items). TopCar S.r.l., born in 1980, also operates in the auto spare parts sector, distributing about 75 thousand references among the most important brands on the international scene. Finally, SARCO, the longest-lived of the group, has been operating in the spare parts sector since the early 1960s, first as a manufacturer and then as a distributor, putting itself forward as a leader in the Silencers and Catalytic converters, Thermal, Hydraulics and Friction, Tuning and Accessories lines.
Before the corporate merger, all spare parts were handled in separate warehouses. The customer’s goal, however, was to channel all products, about 100,000 codes, specifically those of Ricauto and SARCO, into one new building. Originally, within the old warehouses, all activities were carried out manually by operators (picking by order): from product picking to transportation to order preparation for shipment. This mechanism, however, created quite a few problems, most importantly, it greatly fatigued the operators involved with possible occupational injuries. In the face of this, the customer therefore decided to automate the entire process and contact LCS.
The realized solution was thoroughly researched and analyzed together with a consultant and a shelving supplier that the client had previously approached.
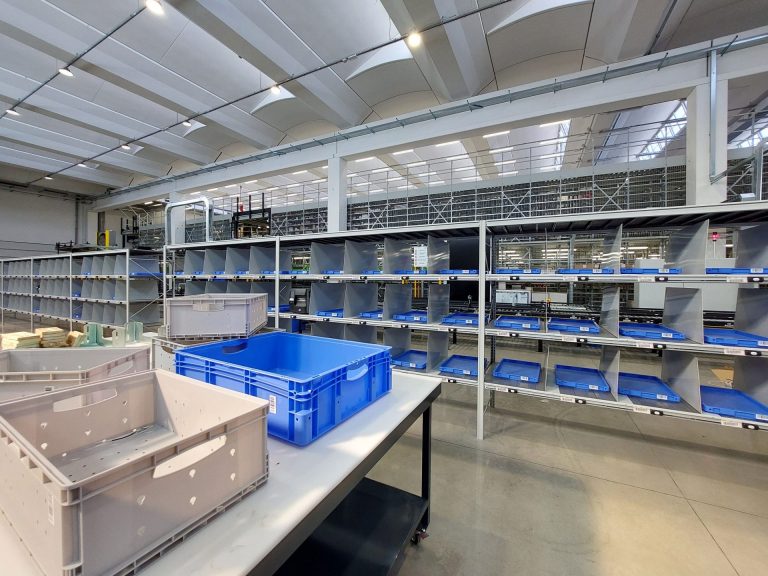
The two phases of the project
Phase 1: Box handling line and packing area
The new building has an overall height of 9 meters and is divided into several floors: ground floor, first floor and second floor. Each floor is divided into 4 work zones with 4 operators, where each operator is responsible for massive picking within his area of responsibility.
The individual operator, after performing the picking steps guided by the WMS, deposits the product inside one of the two types of pre-prepared totes indicated by the WMS, each with its own recognition barcode. These totes are on their own line of responsibility, called the “green” line. Automating the warehouse has therefore made it possible to switch from the manual mode of picking by individual order, to massive picking based on the pick list indicated by the WMS software. The “green” line has a possible accumulation of 4 totes regardless of the type of totes used: 600×400 or 800×600. This operation is repeated for all three floors within the four zones present, for a total of 12 massive picking zones.
A key requirement of the project was then to keep the escape routes clear at all levels. For this reason, the handling lines were built at an elevation of 2220mm. The elevated handling lines, which are located on the ground floor, called the “orange” lines, are connected to all the green lines on the various floors by the presence of 4 elevators. Before the tote conveys to the orange line through the elevators, a height check is carried out; this is to prevent that when the cassette is at height, it gets stuck by bumping against the mezzanine located above it. Therefore, if the height is not in accordance, the line will block and the operator must check and restore the contents.
Once the totes have been deposited and checked on the relevant “green” lines, they convey to the “orange” lines. These lines, coming from the 4 zones, merge into a single line at an elevation of 3200mm before meeting a continuous descender, which takes the cassettes to 700/800mm.
The boxes, therefore, go out with all the mixed products inside, picked up by the operators in the 12 zones. After that, thanks to the reading of the barcode placed on each of them, the cassettes are conveyed to the 6 outupts present, according to the correct destination. In the various exits, there are several operators who pick up the cassette and, guided by the software, proceed to ventilate the order in the cabinets, which feature a Put to light system.
During periods with fewer orders, for example in the afternoon, 2 to 3 operators may be employed, while during periods with a high number of orders, for example in the morning, there may be as many as 5 or 6 pickers. Each of them deputed to order ventilation must enter their credentials into the system through username and password. Once this step is done, each one is associated with a unique color that lights up the various cells in the cabinet to prevent confusion among operators during the high production period.
The cabinet consists of 210 cells open on two sides, and each cell corresponds to a specific customer. Inside these cells are trays on which items are deposited for order preparation. When the system recognizes that the order is complete, a green light turns on at the opposite side of the cabinet where other operators are located, in charge of order preparation. When the order is complete, the goods are placed on a pallet destined for shipment.
Once the tote is emptied, it is manually placed on a dedicated line. After the barcode is read and it is determined that the order has indeed been completed, the tote is conveyed to one of two stackers present, each for the two types of cassettes present. Once 6 cassettes are stacked, they converge to a dedicated exit from which they are picked and deposited on a pallet to return to the various floors for new picking operations, or transported to the tote refilling line called the “Blue Line“.
There are then two additional exits on the ground floor that can go beyond the order ventilation area:
- Single-origin order exit: all packages or totes containing items intended for single-product orders can arrive in this line.
- Counter order exit: inside the warehouse is a store where a customer can directly order items
Finally, in the south area of the warehouse, on the ground floor, are bulky materials that, due to their size, cannot be deposited inside the two types of boxes. These items pass the order ventilation area and are conveyed to the packing stations.
Phase 2: Refilling line
Also in the area on the south side of the warehouse is the area dedicated to refilling the items in the totes. As previously described, the stacked empty cassettes can be transported either on a pallet back to the various floors directly or on the cassette refilling line called the “Blue Line”.
All incoming material from outside is first checked and then placed inside an empty tote that is on the line. The tote is scanned for product-tote association and its weight is checked.
If noncompliant it is discarded and routed to a dedicated line, but if it is suitable for storage it proceeds to a lifter that transports it directly to the second floor using an elevated line. The tote then proceeds to another lifter who can unload it on the second floor or down to the floors below depending on its location. The dedicated operator, with the help of the WMS, picks up the cassette and distributes the various items to their correct locations.
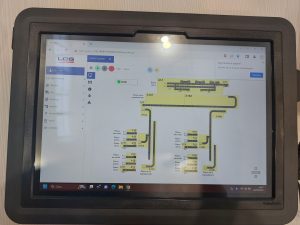
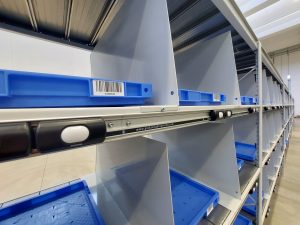
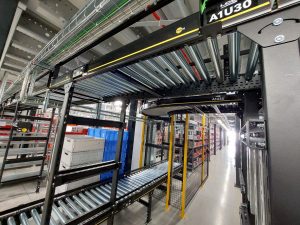
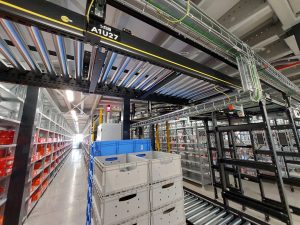
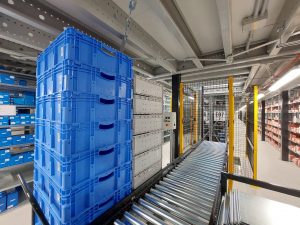
The software
After detailing the various phases of the project, we turn our attention to the WMS system, the heart of the entire system. LCS’s software, WMS LogiWare supports most of the tasks performed within the warehouse. The main tasks of the software include:
- Warehouse mapping with management of logical associations between positions and items
- Profiling of all items in the warehouse
- Creation of picking lists
- Creation of order list
- Location of material in the warehouse: for each UDC, the WMS will create loading lists sorted by location
- Management of order ventilation zone with put-to-light system
- Shipment management
- Interface with corporate ERP system
The LogiCon system, on the other hand, allows supervision and control of the entire automated system by interfacing with the LogiWare system.
Benefits obtained
The benefits and advantages derived from such a solution were immediately tangible; specifically, it was possible to observe:
- Space optimization
- Speeding up operations
- Increased storage capacity
- Reduced lead time in order fulfillment
- Readiness of the plant for future expansions
- Attention to the ergonomics of working activities
- Increased safety
Technical data
- Warehouse height 9 meters divided into three floors: ground floor, first floor and second floor
- Each floor divided into 4 areas of responsibility with 4 operators and as many line loading stations on each floor
- Conveying boxes of two types: 600×400 and 800×600, both with height 220 (max product height 400mm)
- Management of 100.000 product codes
- Transition from picking by order to massive picking
- Plant built in two phases:
- Phase 1: “Green” Handling Lines: the operator places the box after “batch picking”
- Phase 1: “Orange” Handling Line: overhead totes transport line at 2220mm elevation
- Phase 1: “Order ventilation” Line: totes conveying line with order venting.
- Phase 1: Cabinets with “put to light” system.
- Phase 2: “Blue” Handling line: totes refilling line with arrival of new materials
- Plant capacity Phase 1: 500 totes/h
- Plant capacity Phase 2: 150 totes/h
- resence of no. 8 descenders/elevators.
- Order ventilation area with put-to-light system and possibility of handling 210 customers
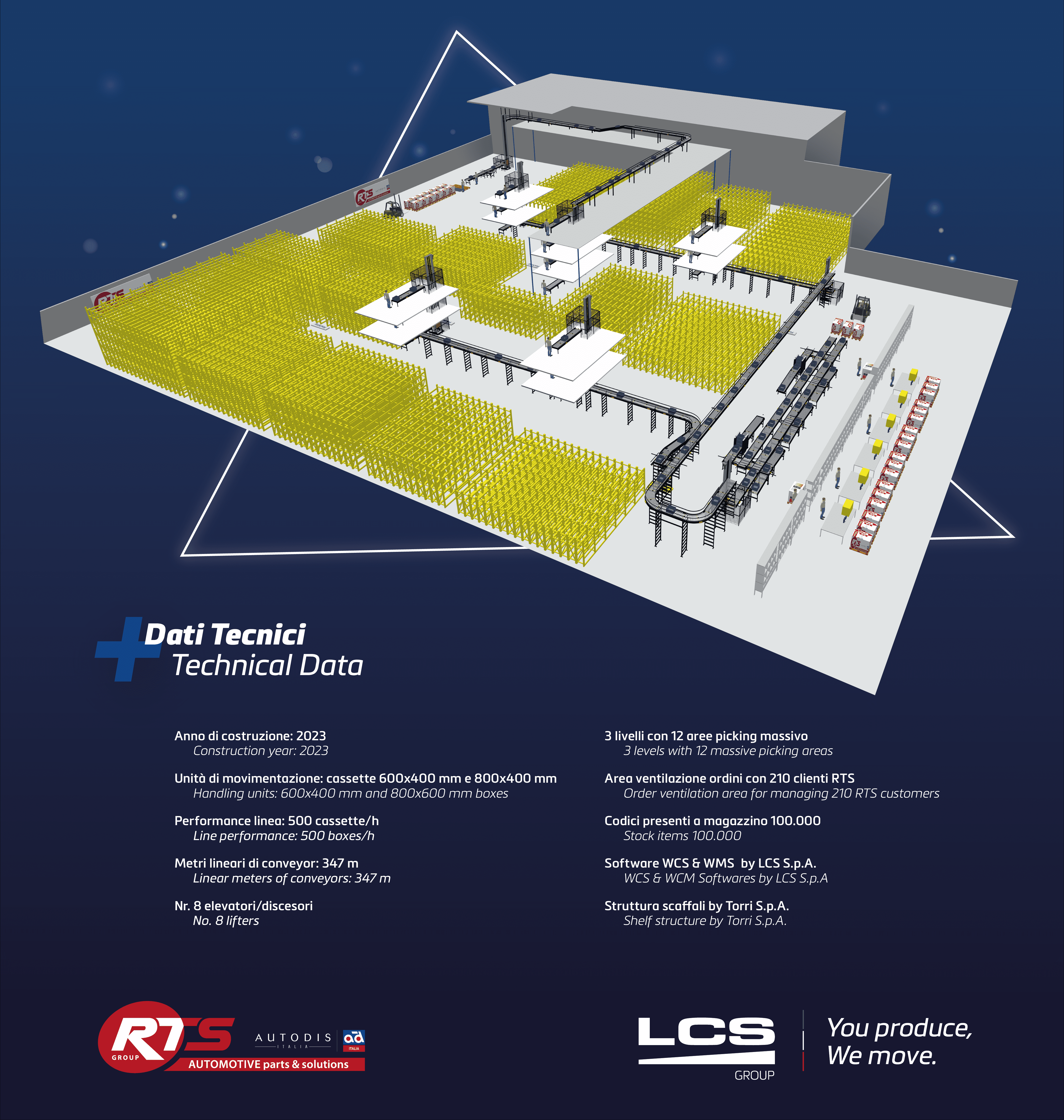