Cimberio – The new Smart Factory 4.0
- Home
- Case Studies
- CIMBERIO – The new Smart Factory 4.0
The new Cimberio's Smart Factory
LCS created an automatic “green field” warehouse for Cimberio in direct connection with production and company management (ERP) in order to support the constant growth of the company.
Cimberio is a historic company among the many companies born from the genius of Italian entrepreneurs. In 1957 the company was founded by Cav. Giacomo Cimberio. Today the Cav. Uff. Giacomo Cimberio SpA, world leader in the production of valves and brass components for the thermo-hydraulic, air-conditioning, gas and water distribution nets, from its headquarters in S. Maurizio d’Opaglio (NO), daily offers the market more than 100 thousand pieces for a total production of over 22 million pieces.
With a turnover greater than 50 million euros and the production entirely concentrated in the factories of San Maurizio d’Opaglio (NO) and Berzonno di Pogno (NO), they employ 190 people and have an international presence with 6 foreign branches that distribute in 77 countries the products of the company located in San Maurizio d’Opaglio. A production that is inspired by the deepest values that the founder of the company handed down to his sons who today manage the company well beyond the national borders.
On this basis, Cimberio entrusted LCS with the design of a new warehouse to increase storage capacity and at the same time to digitize and to optimize the production and the internal logistics processes. The new warehouse will also free up a considerable area of the site which will be dedicated to the increase of the production facilities and it will update and make more efficient the computerization of the factory processes, in addition to the storage ones.
With reference to the intralogistics area (warehouse), the priority was to optimize the space, in order to recover useful surface for new production islands and new offices. Concerning the production areas, the objectives to be met were the following ones:
- Track the most significant data of each work order (OdL)
- Make manual declarations of production operators
- Monitor the system status, the progress of the work orders, the operators allocated on the machines and the production times.
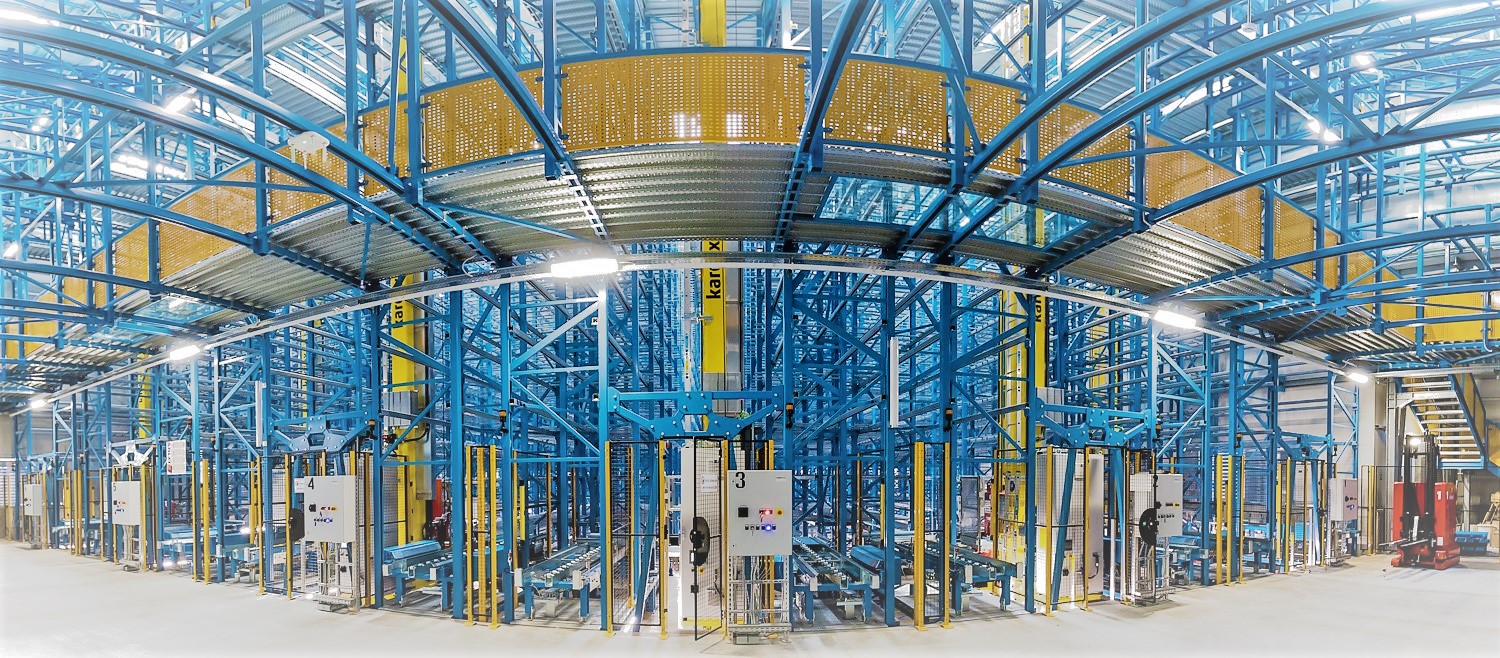
The realized project
The analysis of the production and the distribution flows led LCS to design, engineering and construction of a “green field” plant.
The automatic warehouse has a self-supporting structure 14 meters high with 6 corridors served by as many stacker cranes for metal containers up to 600 kg, for Euro pallets up to 1 ton and for half pallets for a total of almost 14,400 locations.
The storage takes place in double depth for the metal containers and the half pallets, in single depth for the pallets. It is very interesting the plant dedicated to the handling of inbound and outbound goods in the new Cimberio’s warehouse operated by 5 laser-guided LGV trolleys.
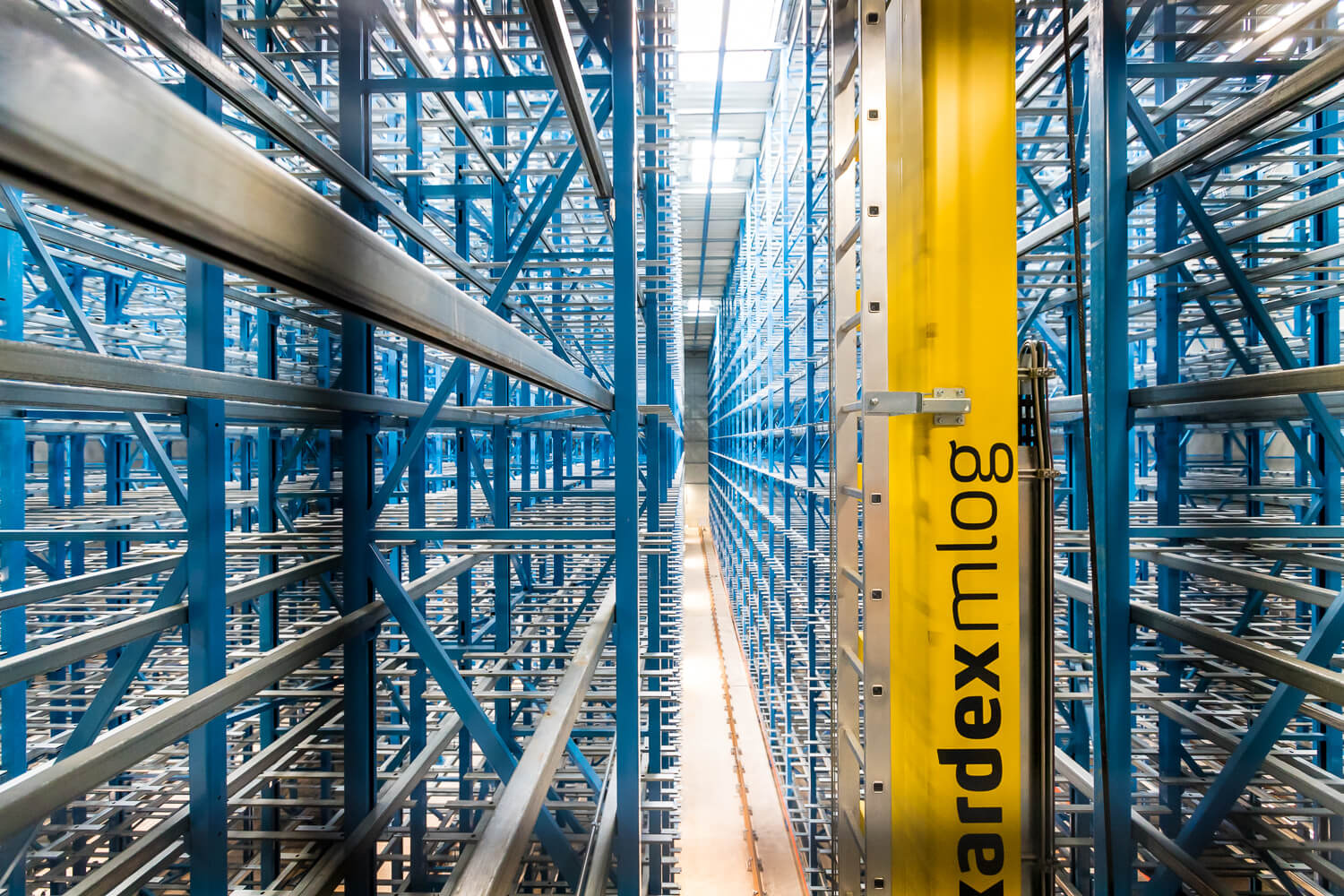
The goods reception area is equipped with adequate technology for checking the size and the weight of the containers of incoming goods to avoid subsequent problems in handling.
The real heart of the plant is the software that LCS has customized for the Cimberio’s warehouse. The WMS management software with a wide range of consolidated functions, created by LCS software development department, determines the entire operation of the warehouse and harmonizes it with the rest of the company in perfect 4.0 logic.
The M.E.S. (Manufacturing Execution System) is also originally developed by LCS and it harmonises and coordinates the production management of the S. Maurizio site and the neighboring one of Berzonno di Pogno.
Such software:
- is in direct connection with the in-house ERP
- provides the production recipes to the production islands in real time
- returns information for the monitoring and the progress of the production orders.
Furthermore, the analysis and the processing of the final data allow to determine quickly and accurately the performance of the production system by generating the reference KPI.
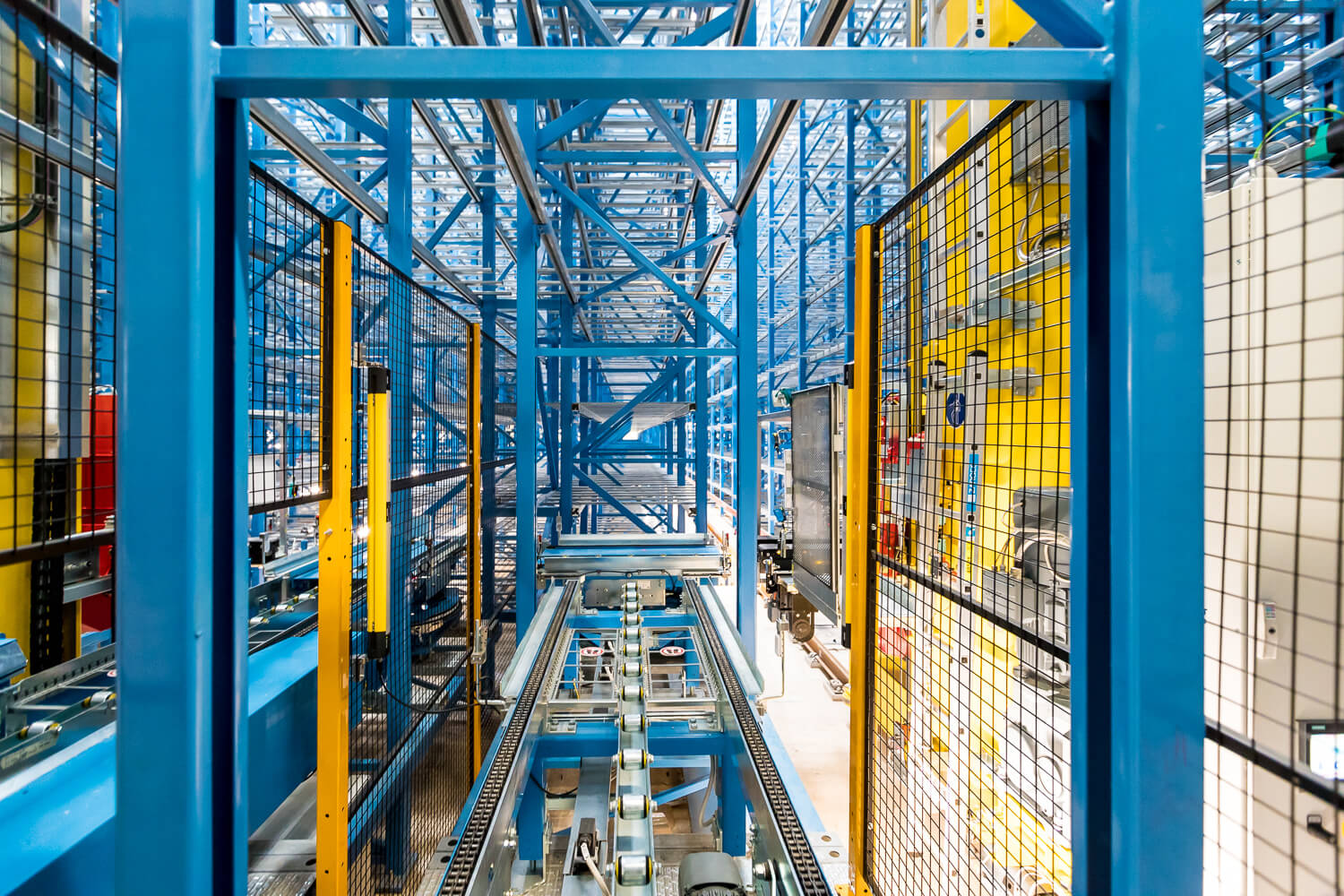
Obtained benefits
The new 4.0 system created by LCS has allowed Cimberio to manage production and intralogistics processes more efficiently, by reducing the capital employed in the production cycle and the lead time in order fulfillment.
- Reduction of errors thanks to automation
- Ergonomics thanks to “goods to man” and the new picking stations
The interconnection among the production machines, the automatic warehouse and ERP allows to control the entire factory from a single central unit, from the arrival of the goods in the warehouse up to the shipment.
In this way, all processes are automatically tracked and the data are automatically historicized and reviewed in view of a constant improvement in the strategic choices of the company.
LCS was able to create this innovative plant thanks to the special cooperation with the Cimberio’s team, by sharing the company’s core values: innovation, excellence, sustainability.
- Innovation because the new Cimberio’s warehouse is technologically advanced and prepared to support the technological evolution over time.
- Excellence for LCS means not only extraordinary quality of products and systems in the new plant but it also means irreproachability in project management and related services.
- Sustainability for LCS means a plant with a low environmental impact and respectful of energy consumption in general. A flagship for LCS that will support Cimberio in their unstoppable growth.