Galbusera – Revamping of stacker cranes and new pallet handling system
- Home
- Case Studies
- GALBUSERA – Revamping of stacker cranes and new pallet handling system
LCS carries out revamping interventions for Galbusera on 4 existing stacker cranes and allows to optimize operational flows by implementing a new pallet handling system.
The company and the needs:
Founded in Morbegno in 1938, Galbusera SpA is an Italian food company also active abroad, which produces biscuits, crackers and snacks. For over 70 years the company has been based on values such as: customer focus, respect and transparency and has always sought excellence in the quality of raw materials.
The interventions carried out by LCS were concentrated at the production site in Cosio Valtellino, in the province of Sondrio and were carried out between the end of 2019 and the beginning of 2020.
Galbusera’s main objective was to enhance the investments made in the past and decongest the shipping area of the warehouse by intervening in 4 strategic points of the warehouse and more precisely:
- Modernize the 4 stacker cranes of the existing automatic warehouse
- Automate the entry of pallets arriving from production to the automatic warehouse, speeding up operations
- Automatically stack the pallets arriving from production destined for shipment
- Automate the exit of whole pallets from the automatic warehouse by conveying them to a single pick-up point for loading them onto the means of transport.
LCS was therefore entrusted with the task of carrying out revamping interventions on four stacker cranes already existing in the plant and implementing a new pallet handling system.
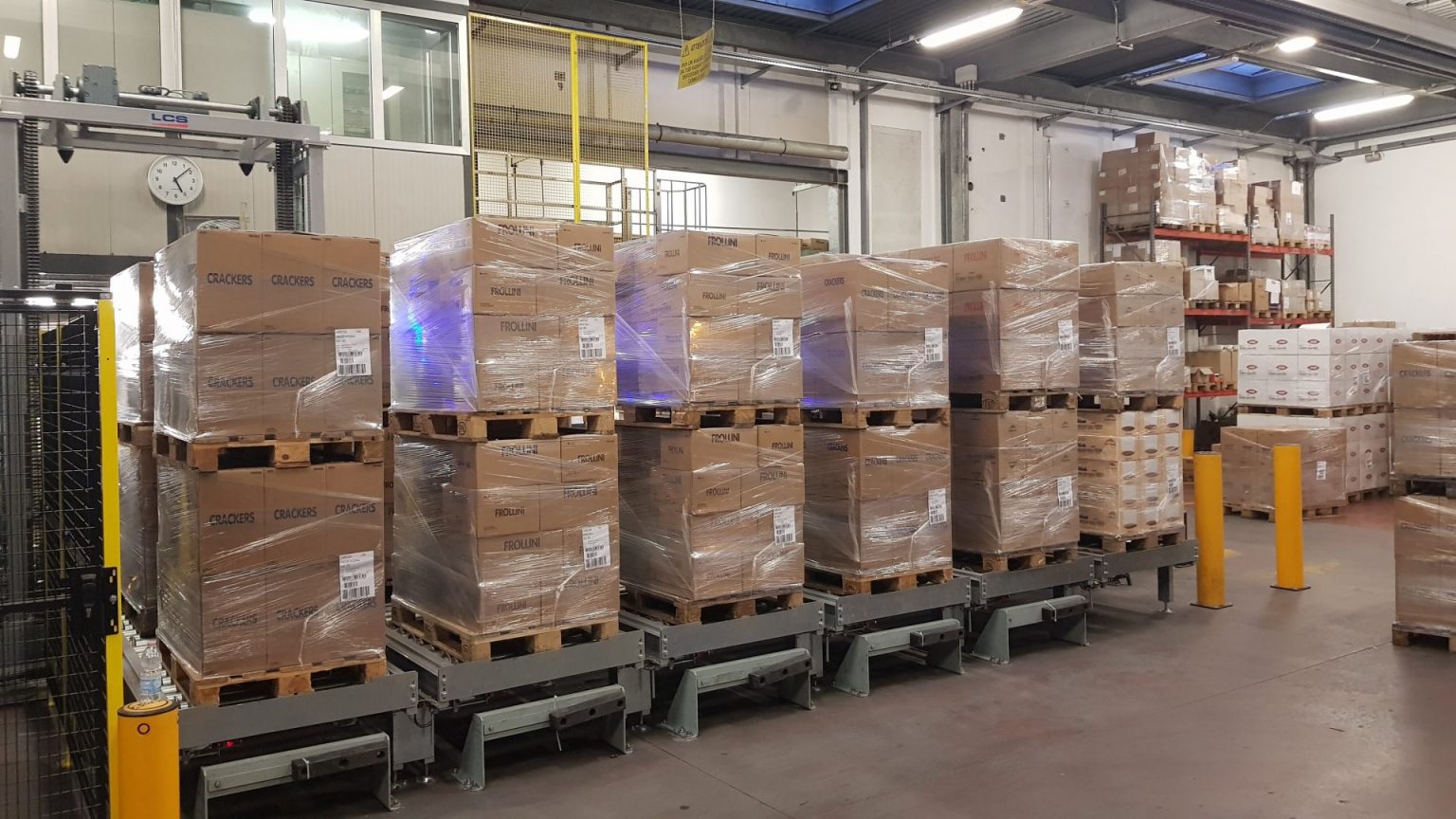
The project
As anticipated, the modernization interventions concerned the four stacker cranes already present in the plant. On two machines the direct current motors were replaced, relating to translation and lifting, while the following interventions were carried out on all four:
- Replacement of the electrical panels on the machine (LCS Automation)
- Insertion of new drives
- Insertion of cameras for ground view of the fork group
- Revision of the safety circuit: regulatory standards
- PLC for automation and safety control
- New development of the automation software: use of our LogiTRASLO software to control the stacker cranes and adapted to the particularities of the system
- WCS supervision software: installation of our LogiCON software for the supervision and control of the entire system
- WMS management software: update of our LogiWare software for automatic warehouse management
The new pallet handling system:
- Pallets arriving from production and destined for automatic warehouse or shipment
The pallets coming from the production on the roller conveyors are identified by a barcode reader, automatically labeled and dimensionally verified by a shape control system.
Based on their destination, the conveyor system directs them to the automatic warehouse or to the shipment. In case of an anomaly in the verification phase, the pallets in question are discarded in a dedicated location.
- Pallets intended for shipment
The pallets intended for shipment are automatically stacked for the same article in 6 different positions by a shuttle with telescopic forks and lifting. Once stacked, the pallets are made available to forklift drivers to be loaded onto vehicles.
- Pallets from production to the automatic warehouse
The pallets destined for the automatic warehouse are brought to a height (about 3.5 meters) by means of an elevator and sorted by means of a shuttle to the 4 conveyors at the entrance to the warehouse to be taken by the stacker cranes and stocked.
- Pallets from automatic warehouse to shipment
The pallets coming from the warehouse are deposited by the 4 stacker cranes on the chain conveyors. By means of a roller backbone they are conveyed to the dedicated station, from which they are picked up by forklift drivers and loaded directly onto the vehicles.
The Software:
The automatic functionality of the control of the motors of the transport system is given by means of the online connection with the LCS LogiCON supervision system. In this mode, the PLC system executes the transport commands received, independently managing the tracking of the pallets.
The LogiCON system allows supervision and control of the complete system in automatic local and automatic online operation connected to the LogiWare warehouse management WMS system.
Benefits
The interventions carried out by LCS for the modernization and design from scratch of the pallet handling system have led to the following benefits:
- Enhancement of past investments
- Decongestion of the shipping and vehicle loading area
- Elimination of low added value activities through the introduction of automation
- Speed up of operations
- Greater safety in the shipping area
- Greater control over activities
- Process automation for pallet management
- Greater continuity in the workflow
- Efficiency of the entire system thanks to the new automation software installed
- Greater availability of the entire automatic system thanks to the real-time display of the system status (cameras / WCS software)