Cadel – The New Integrated Factory
- Home
- Case Studies
- CADEL – The New Integrated Factory
The company and the needs
Founded in 1949, Cadel is an Italian company that designs and builds quality stoves. It became part of the MCZ Group in 2013 and offers a complete range of ventilated, ducted and hydro pellet stoves. For over sixty years, it has interpreted the needs and requirements of families, producing a variety of products with distinctive designs that are affordable and easy to use. A Made in Italy company that maintains the values of tradition by looking to the future.
This constant focus on progress required the design of a new production site. In fact, the new Integrated Factory in Santa Lucia di Piave (TV) was built to support the company’s constant growth. The 4.0 solution is not only highly technological, reliable and cutting-edge, but also scalable over time. In fact, a flexible system has been designed and implemented, capable of satisfying continuously changing needs and possible future expansion.
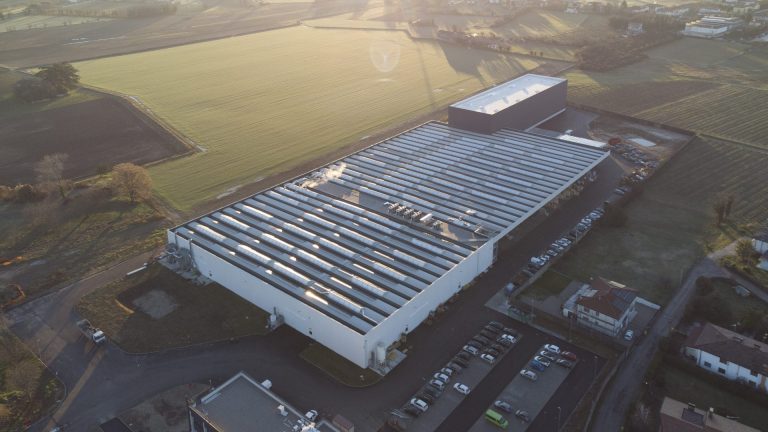
The realized project
As a result of the analyses performed, LCS engineered a 4.0 solution that includes an automatic warehouse, 10 production lines, 8 finishing lines and a plant consisting of 9 AGVs.
The new pole, which has an area around 18.000 sm, serves the entire production process for the construction of the final product. From the raw material to the construction and customisation of the stove on the production and finishing lines, to storage in the automated warehouse and finally to shipment to retailers and/or large-scale retail trade.
Within the new factory several workflows develop, which can be broken down as follows:
- Semi-finished products, coming from the production lines are stored in the warehouse or converge from the warehouse to the finishing lines.
- The finished product, coming from the finishing lines, is stored in the warehouse
- The finished product is destined for customisation and then stored in the warehouse ready for shipment
- Assembly kits, sourced from external suppliers, are intended for customisation or storage
- The finished product is destined for shipment
Automatic warehouse and AGV system
The automateic warehouse has a 21-metre high self-supporting structure with 10 storage levels, 3 aisles served by as many stacker cranes for a total stock of almost 17,300 locations reserved for the seven types of loading unit present.
Storage takes place in double depth for pallets and in quadruple depth for half pallets.
The project is designed so that the warehouse can be expanded in the future and the storage capacity can be increased to over 23,000 locations.
On each input to the warehouse there is a gauge control, while on each ouput there are two labelling machines for labelling pallets destined for shipment.
The automatic warehouse is connected to the different areas of the factory by a fleet of 9 AGVs that move thanks to an induction system embedded in the floor. This contactless power transfer not only allows the vehicles to be driven and powered while moving, but also provides benefits in terms of environmental sustainability through the elimination of lithium batteries (management and disposal).
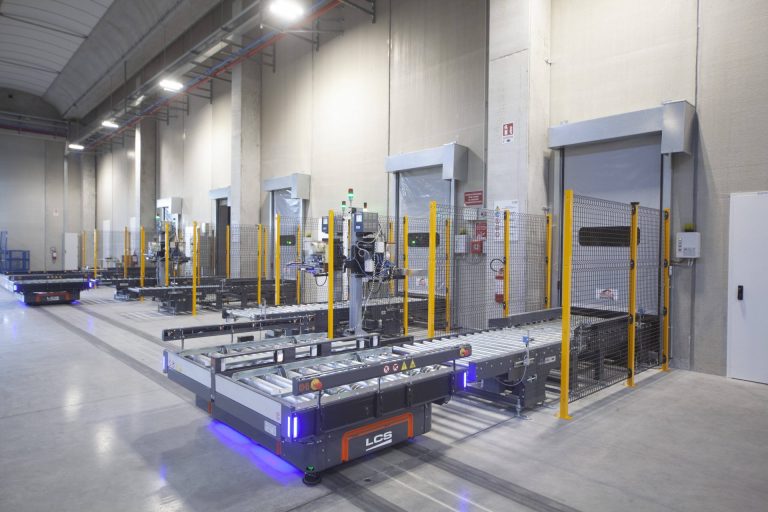
Production lines
The stoves are produced on 10 assembly lines for semi-finished products, 7 lines for product finishing and 1 line for kitting (customisation).
The assembly lines are configured in such a way as to be able to subdivide the various assembly phases up to a maximum of 6 operators, while the finishing and assembly lines are configured in such a way as to have a short line, with 1 operator, and a long line, with 2 operators each.
All lines are configurable and managed by the LCS software according to the type of stove to be produced.
The software
To enable the customer to track the pallets handled and minimise human errors resulting from pallet identification and ground handling operations, was implemented an articulated system of RFID readers installed at all entry and exit points to the system and managed by LCS Software.
The pallets are labelled with barcodes and RFID tags, applied by the first operator of each assembly line according to the production order, and checked at each production step, from assembly to finishing, from storage to shipment.
Real-time traceability of materials handled within the plant is therefore guaranteed.
The serial number of the stove, and with it the components that make it up, are associated with the RFID tag by the company’s information system, ensuring the traceability of materials even after delivery to the customer.
RFID gates have also been installed on the docking flaps of the transport vehicles, through which the correct loading of the trucks is certified.
This also allows logistics to quickly and efficiently check the loading and closing of travel documents, before the trucks leave the plant.
The LogiWare WMS software manages, in direct connection with the customer’s ERP, the entire automatic warehouse, while the LogiCon/LogiDrive system, connected to the LogiWare system, allows supervision and control of the entire plant.
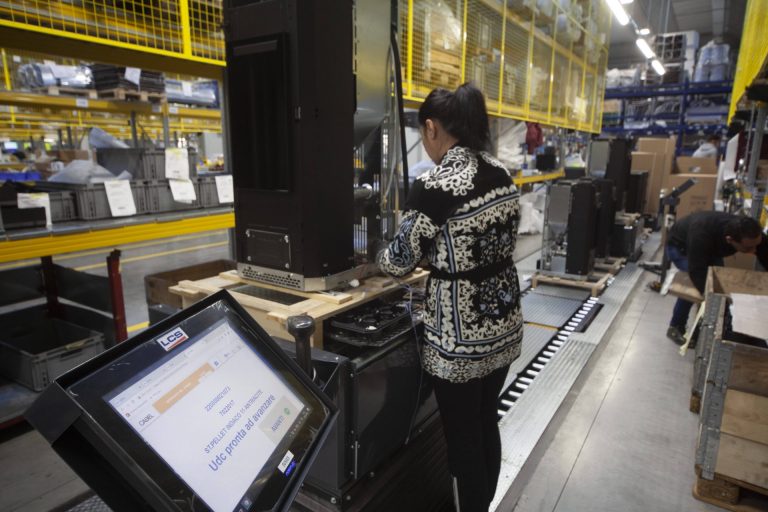
Benefits obtained
With the customer, a real Intelligent Factory in a 4.0 perspective was designed and implemented, resulting in immediately tangible benefits and improvements:
- Integration of the entire stove production process in a single site;
- Increased production efficiency and workflow management;
- Constant traceability and control of loading units via RFID system;
- Optimization of space and increased storage capacity;
- Automation in the handling of goods;
- Significant cost reduction.