Bisio progetti – 4.0 technology in mobile robotics
- Home
- Case Studies
- BISIO PROGETTI – 4.0 technology in mobile robotics
The LCS project allowed the integration of new 4.0 paradigms with the aim of optimizing efficiency and flexibility, ensuring continuity and safety.
The Company and the needs
Bisio Progetti is an Italian company that deals with molds and processing of plastic material for third parties, with headquarters and production site in Alessandria. In 1990, following a merger operation, it incorporated a plastic material molding and processing company (R3 Srl) and became part of a well-known industrial group in Italy and in the world, Guala spa, operating in the sector of warranty closures for spirits, toothpaste dispensers and triggers.
Over the years, the company has developed a strong technological know-how in the research and design of molds for new products conceived with technologies of materials and shapes that are able to meet the needs of the constantly evolving market. One of these is the production of capsules for coffee and other beverages, which the company is able to satisfy thanks to a catalog of capsules suitable for the requests of each type of order.
The continuous growth of requests and the need to ensure maximum continuity of operations, has pushed the Bisio Progetti company to rethink at 360° intralogistic handling flow with a solution that would allow to exploit 4.0 technologies, integrating hardware and adding value to the production flow in full continuity and safety of operations.
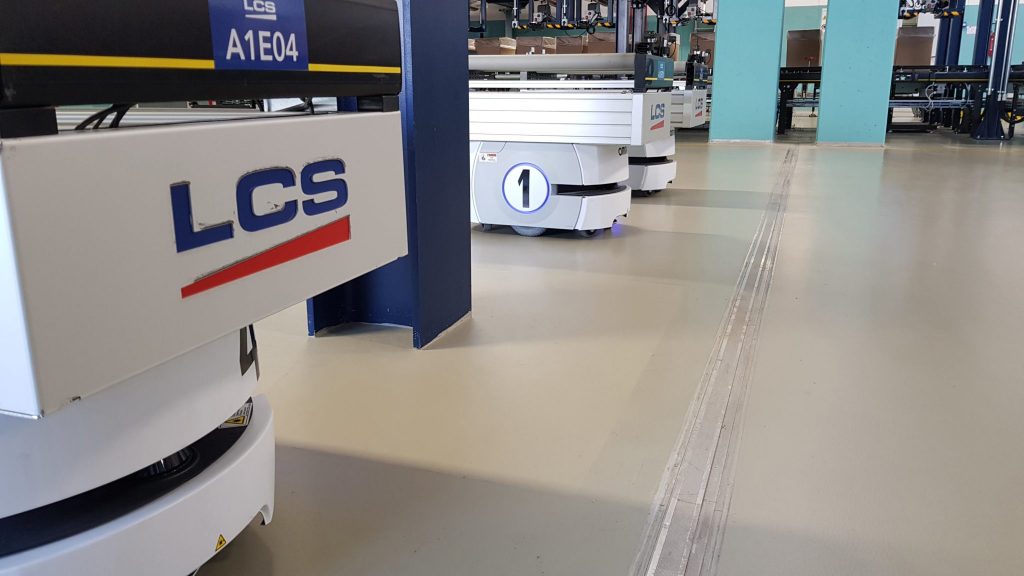
The solution
LCS, thanks to its technological partnership with Omron, based the project on mobile robots, called AMR (Autonomous Mobile Robots). These robots represent an advancement compared to traditional AGVs as they do not require costly additions to the existing layout but navigate independently, each time calculating the most suitable path to satisfy handling requests based on their position. In addition, this technology uses laser sensors and integrated cameras to extrapolate data in real time on the path and process them thanks to Artificial Intelligence to avoid fixed or moving obstacles.
To meet a peak demand of 210 boxes / h, a fleet of 7 AMRs was introduced. At each cycle, the robot feeds a machine with an empty carton and loads a full carton to then transport it to the closing area. They have an autonomy of 8h and to guarantee maximum availability during operations, they independently manage their recharging: upon reaching the minimum battery autonomy threshold they go to the dedicated area of battery change, where an operator will replace it with one totally charge. The robots are equipped with an automated roller conveyor that allows easy alignment with the other roller conveyors downstream of the forming and filling machines and the system for automatic box closing.
The system is coordinated by the LCS LogiCon supervision software, which organizes the fleet of robots and interfaces with the MES in order to select the most suitable robot for its handling at the stations for each handling request. Once a box has been filled at a station, a request is sent to the central node to recall a new request to be fulfilled. The system collects all the requests from the stations and prioritizes them based on the queue of requests to be completed, the speed of the filling stations and the urgency of the order related to the request. Once the most suitable one has been selected, the central node queries all the robots to find out their status, i.e. if they are available to carry out a new mission or if they are still engaged in the previous one. The request is then sent to the selected robot which calculates the optimal path to fulfill the request. At the end of the request, the robot notifies the central node of the completed mission. The central node efficiently integrates the robot fleet with real-time station requests to ensure maximum continuity of operations and reduce errors.
Obtained benefits
This automation project is an example of intelligent and flexible handling that uses cutting-edge technologies from an industry 4.0 perspective.
- Reduction of machine downtime due to lack of materials and handling errors, thanks to the high availability and reliability, precision and reduced handling times of the robots
- Improvement of the management of production areas and the possibility of employing operators on activities that require human skills (supervision and improvement of processes).
- Increased safety in the layout area dedicated to handling thanks to safe handling systems.