K + N – Iveco | Spare parts warehouse, in step with the times
- Home
- Case Studies
- K + N – IVECO | Spare parts warehouse, in step with the times
Iveco spare parts warehouse, in step with the times
Since 1997 … revamping the automatic warehouse to meet the new market requirements.
The design and implementation of Iveco spare parts automated warehouse in headquarters in Turin dates back to 1997.
The warehouse was very different from the current one, especially if we compare the ratio pieces / lines / order and processing times.
During these years, in fact, Kuehne + Nagel has adapted the automated warehouse to the new market requirements, carrying out some interventions at various levels, from mechanical to software.
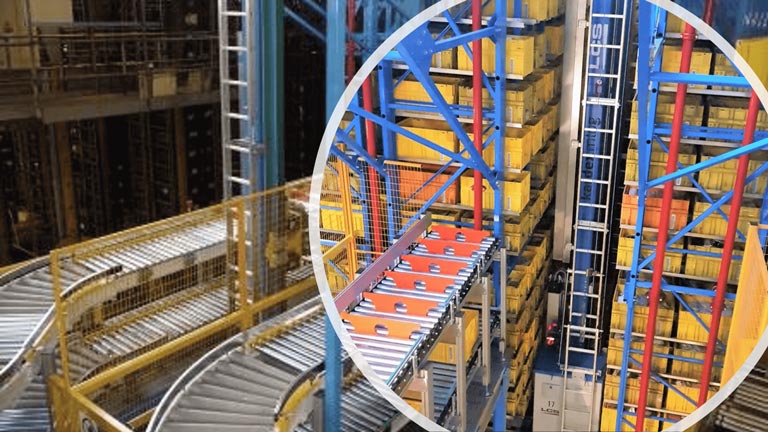
The old warehouse
The automatic system realized in 1997 was composed by the following components:
- 4 stacker cranes equipped with 3 gripping means each for storing articles of Class B and C placed in boxes type Odette 40x60xH30 with maximum weight of 50 kg; length corridor of 150 meters. Height of the stacker cranes of 10 meters. Static capacity of approximately 45,000 boxes ” Odette ” with dimensions of 400x600xH300 and maximum weight of 50 kg
- 4 stacker cranes equipped with a gripping means each for the storage of class A articles palced in boxes type Odette from 40x60xH30 with max weight of 50 Kg; corridor length 20 meters . Height of the stacker cranes of 10 meters. Static capacity of approximately 3,500 boxes ” Odette ” with dimensions of 400x600xH300 and maximum weight of 50 kg
- 12 single- order picking bays
- 4 shipping parcels construction bays
Details
LCS has created a solution based on the need to cope with an increase in daily orders and therefore the need to manage them, without interrupting the workflow, with the following solutions:
- Renewal of the PLC, WMS and WCS software department;
- New corridors with stacker cranes;
- New entrance bays.
Benefits
The solutions implemented represent for the Customer an important technological advancement that has allowed to obtain the expected benefits and improvements:
- Increased dynamic capacity,
- Better stock performance,
- Increasing daily shipments,
- Greater storage capacity,
Implementation and Adjustment steps
After warehouse realization in 1997, where LCS participated as automation software provider, the company has always worked for service activities on the system. The first important adjustment was carried out in 2008-2009, when LCS “renewed” the automation software (PLC) of the entire transport cassette system, the system control / monitoring software (WCS) and the automated warehouse management software (WMS), introducing improvements at all levels to increase the system store performance.
The Second Adjustment
A challenge not easy to deal with for two reasons:
- warehouse operation, from 06 to 24 from Monday to Friday, and from 06 to 14 on Saturday
- no interruption in operations allowed for testing activities and system start-up
The second adjustment/extension was carried out in 2010-2011, as the system was no longer able to respond to the continuous increase of the daily shipments in terms of levy rows. As a result, 2 new corridors with relative stacker cranes equipped with 3 gripping means each were joined to the 4 existing corridors with a length of 150 meters. Furthermore, different mechanical interventions were made on the entire boxes mechanical handling system to increase the dynamic capacity, picking bays have been reconfigured, both mechanically and in terms of software and a new boxes input bay was made in the warehouse. In addition to the above described activities, electro-mechanical works of adaptation to the entire system regulations were carried out.
This second adjustment has been designed and manufactured entirely by LCS “turnkey ” and it involved the storage racks for boxes, stacker cranes , mechanical components (conveyors) , the electrical installation to get to the adjustment of automation, control and supervision and management software.
The Third Adjustment
The third adjustment/extension was carried out during 2019 in order to enhance and further develop the efficient automatic handling of items placed in crates and conveyed using the “goods to man” method compared to a “traditional” management using the “man to goods” method.
As with the previous extension, the entire project was carried out entirely by LCS in turnkey mode, i.e. in addition to the automation LCS also supplied the shelving.
LCS has therefore developed and implemented an integrated solution consisting of the addition of 2 Mtwini miniload stacker cranes from Kardex Mlog with 3 telescopic fork devices each for the storage of 600×400 mm Odette boxes in double depth, increasing the static storage capacity by approximately 37,500 crates.
The connection between the existing conveyors and the new stacker cranes has been completed by means of a new warehouse front area on two levels (IN/OUT) with roller conveyors and transfer units placed on a platform at a height of 5 metres.
The automation system designed and implemented by LCS
In addition to the Level 1 – electrical part including the design and construction of the electrical cabinets and the electrical system of the stacker cranes and the input/output conveyors of the system, LCS has developed and installed:
- Level 2 – PLC software “LogiTraslo” and “LogiTrasp” for the automation of stacker cranes and conveyors, respectively.
- Level 3 – WCS software “LogiCon” for the Visualization and Supervision of the systems
- Level 4 – “LogiWare” automatic warehouse management software (WMS)
The expansion solution including the 4 levels of automation was developed and implemented by LCS during 2019, with constant management and control of the designated project manager and monthly progress report. All implementation activities were carried out without any downtime. At the end of the implementation, in October, LCS organized 3 days of training for plant operators and maintenance personnel and provided start-up assistance.