Material handling in service of e-commerce
- Home
- Case Studies
- Material handling in service of e-commerce
The Company and the needs:
LCS implements an automated package handling, identification and shipping solution for a customer in the e-commerce field.
The Client is part of a group of successful companies that design, manufacture and distribute lines of clothing and accessories inspired by the most elegant designers. All the brands offered are currently sold within the most prestigious department stores around the world.
The goal of the Client was to implement an automatic system capable of controlling the clothing items, coming from the warehouse inside boxes (identified by a barcode label), and sort them correctly according to the shipping order.
The task of LCS, therefore, was to develop a solution that would automate and make the identification and management of the packages to be associated with orders more reliable, guaranteeing the traceability of the items and eliminating any errors due to manual management.
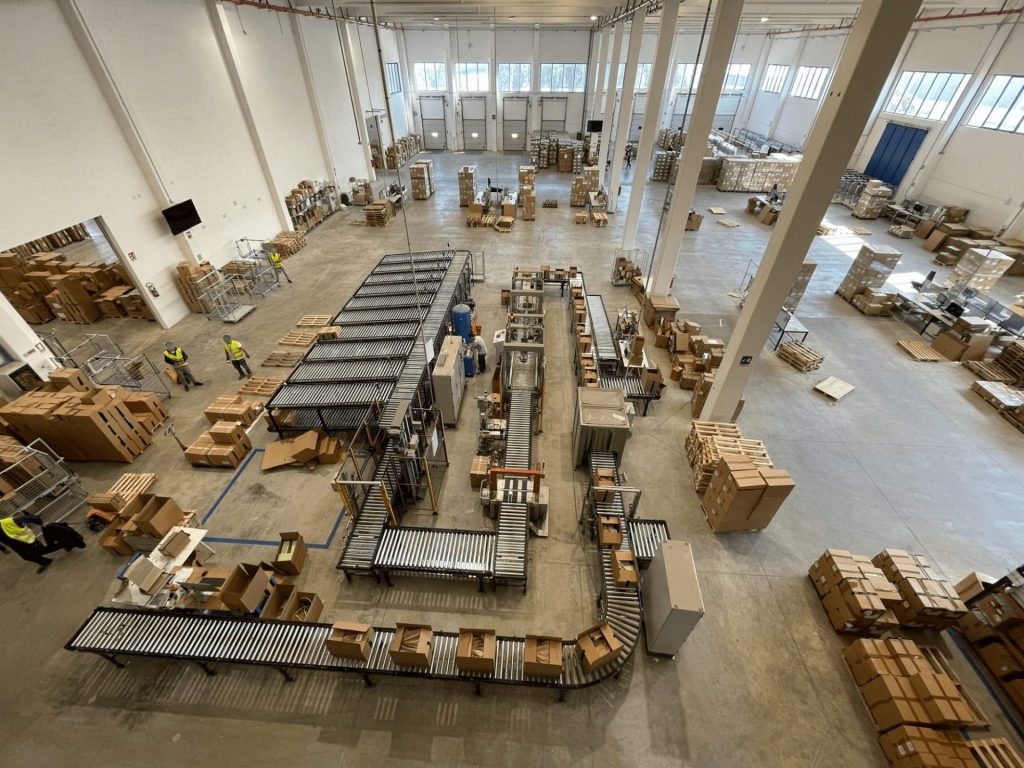
The realized project:
The project developed and implemented by LCS provides an end-of-line system for transporting packages with an initial position used for manual loading of the shipping units.
The operator positions the box on the loading roller conveyor and these automatically advance to the identification and control system. All boxes are equipped with a unique barcorde label that determines their identification and final destination. In addition to identification, through a barcode reader, a check of the dimensions of the package is carried out and the weight recorded.
At this point, the boxes enter an RFID tunnel, all the content is checked and the exact correspondence with the order being processed is verified. At the exit of this system, in the event of an anomaly or non-compliance, the box is diverted to a dedicated exit where an operator removes it and verifies the error.
The compliant boxes continue towards two taping machines that adjust automatically, based on the box format, and close the upper flaps with adhesive tape with two different brands. Before continuing to the sorter, the boxes are strapped and then labeled with the shipping label.
At the end of the line there is a sorting system equipped with 20 outlets on two levels connected by an elevator that sorts the packages to the first or second level according to the final destination. After sorting, the operator places the packages on the pallets in preparation for shipment.
The operation of the automatic system and the traceability of the packages are guaranteed by the LCS LogiCON software, which has the task of controlling and supervising the entire system.
The LCS software interfaces with the customer’s ERP, and checks the correspondence between the goods arriving from the warehouse stock and the items listed for shipment, ensuring maximum accuracy in order preparation.
From an electromechanical point of view, the system is able to manage up to a maximum of 423 LU/ hour of which:
- A part to be closed manually in a dedicated filling station
- A part to be closed automatically with the taping machine 1
- One last to be closed automatically with the taping machine 2
Benefits obtained:
The solution implemented by LCS allowed to:- Increase efficiency in all operations
- Elimination of errors due to manual management
- Optimize resources in a timely manner for each warehouse process
- Relocate people in activities with greater added value thanks to the introduction of automation
- Obtain the traceability of all items and constant control of all processes.